7S管理并不是一个新鲜的话题,也并非一个似乎被神话的多么高端的管理。7S起源于5S,而5S则起源于日本。第二次世界大战后,日本企业将5S运动作为管理工作的基础,推行各种品质管理手法,产品品质得以迅速提升,奠定了经济大国的地位。而在丰田公司的倡导推行下,5S对于塑造企业的形象、降低成本、准时交货、安全生产、高度的标准化、创造令人心旷神怡的工作场所、现场改善等方面发挥了巨大作用,逐渐被各国的管理界所认识。那7S管理到底是什么?
简而言之,7S管理包含了“整理”,重点划分现场“要的”和“不要的”物品;“整顿”,运用定点、定品、定量的“三定”方法,规范现场“要的”物品的管理;“清扫”,时刻保证车间干净卫生;“清洁”,建立管理、评价及考核体系,并定期对前“3S”进行回头看;“素养”,通过制度规范人的言行,养成良好的行为习惯;“安全”,系统开展安全管理,确保人人讲安全、守安全;“节约”,增强节约意识,养成自觉节约时间成本、空间成本、物料成本的好习惯。
看起来并不是很高深的7个“S”,但做起来并不那么容易。然而,全面推行7S管理是目前阳逻厂的迫切需求,我们需要一个更加整齐规范、清爽明亮、人人敬畏的工作环境,需要一个更加遵章守制、富有朝气、充满斗志的团队。笔者认为,长期推行工厂7S管理,需要着重做好以下五个方面工作。
一、建立制度
要建立一套完整的7S管理制度,明确每个“S”的工作内容、实施路径、评判标准、奖惩标准,对于关键环节要做到可视化、可量化,做到即便是新人也一看就懂。要实施区域责任制,把7S管理责任落实到人。
二、做好培训
要开展工厂全员7S管理培训,一方是理论培训,教会大家7S管理的重要意义、基本内涵、动作要领等;另一方面是现场培训,教会大家7S管理制度如何在现场实现。同时,要把好新入职员工的培训关,同“三级”安全教育一起纳入新员工入厂培训内容。再者,要通过7S看板、工厂广播站、7S管理知识竞赛等,进行广泛、深入的宣传。让所有人员都知道为什么做,在哪里做,具体做什么,什么时候做,谁来做,怎么做,做到什么程度。
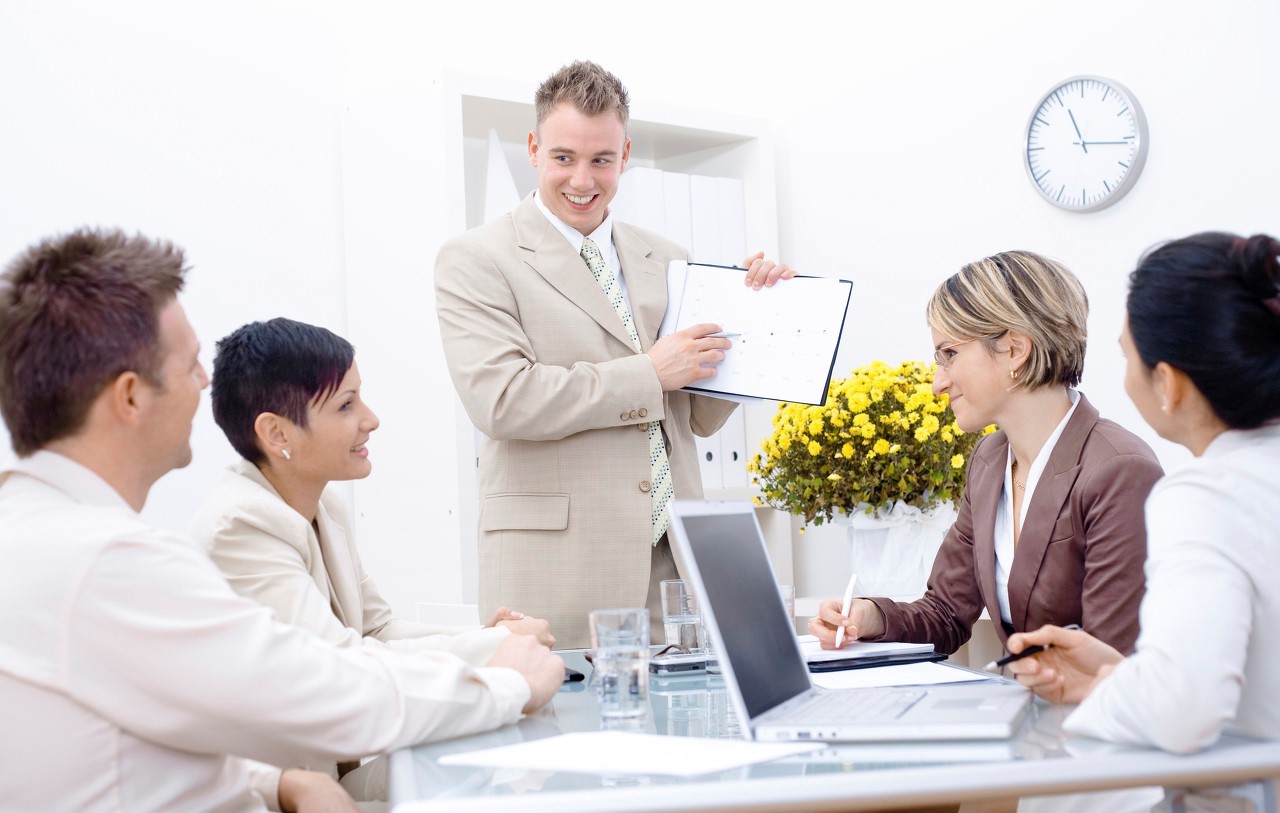
三、转变观念
要敢于向不良的管理方式、生产方式和行为习惯说不,不能以“自己的经验”、“以前就是这样做的”、“不会影响生产大局”、“一线人员忙于生产”等为理由,拒绝改变、拒绝革新。任何事情,一开始就持“无所谓”或者“排斥”的态度,最终都难以成功。公司致力成为受人尊重的科技型投资平台,科技事业部致力成为最具实力的装配式建筑整体服务商,正在全面推进二次创业,工厂作为管理和效益的输出终端,如果连改变不好的环境和习惯的勇气都没有,如何为公司、事业部实现战略目标提供支撑?因此,必须行动,马上行动,像东风本田公司工厂那样,大张旗鼓的开展7S管理。革故鼎新是对创业前辈做好的致敬。
四、加强执行
制度再好、培训再好,缺少强有力的执行力,一切都是空谈。开展7S管理千万不能“磨洋工”,7个“S”是一环套一环,哪个环节出了问题,都不能成功,特别是前面几个“S”,直接影响了后面内容的正常实施。在主观上,各级管理人员要率先垂范,通过实际行动引导产业工人跟着学、跟着做;在客观上,要建立督查组,按周开展监督检查工作,检查结果与管理人员绩效、产业工人收入挂钩,把考核落到实处。总之,要让工厂全员对制度和考核有敬畏之心。
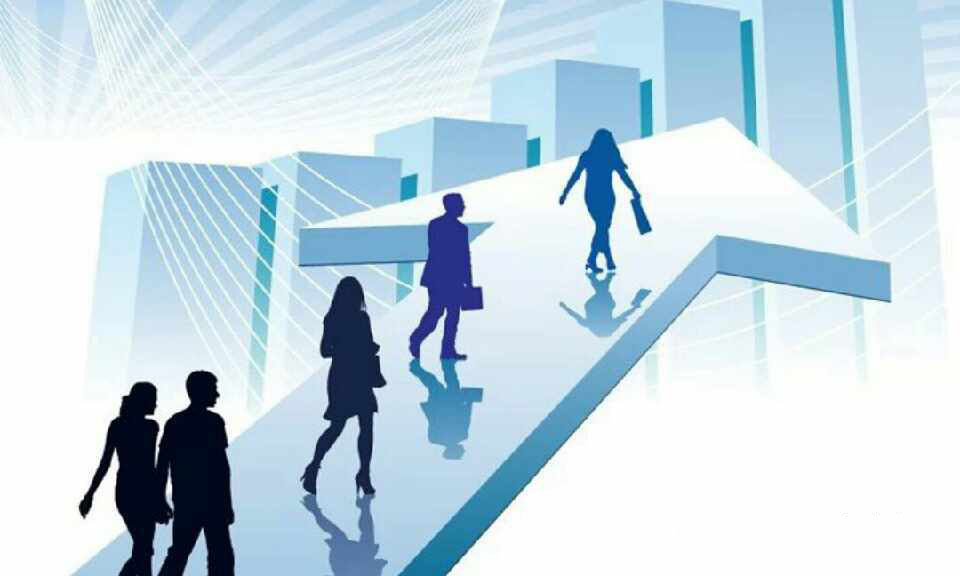
五、保持韧性
实事求是讲,要改变大家习以为常的工作和行为习惯,需要一番努力,并非一日之功,一蹴而就。7S管理要有目标、有步骤的推进,不能因遇到了困难和阻力就放弃,不能让“经验”和“习惯”牵着鼻子走。要像公司副总经理谢俊勇曾在科技事业部2019年第二期企业发展务虚会上说的那样,干事创业就要有斗争精神,要敢于斗争,善于斗争。要想实现7S管理目标,就必须有斗争精神,有管理韧性。
总而言之,工厂7S管理本质上是在规范人的习惯和言行,促进员工综合素质提升,进而提高工厂规范化管理水平。7S管理可以作为革新工厂管理,打造示范工厂的突破口。时不我待,即刻出发。
文章来自网络,版权归作者所有,如有侵权请联系删除
冠卓咨询公司的老师很专业,也很敬业;深入现场了解企业面临的问题及难题、深入现场一线指导项目改善。
———双沟酒业精益六西格玛推进负责人