项目背景:
厦门金龙联合汽车工业有限公司(简称“金龙客车”)成立于1988年,专注于大、中、轻型客车整车研发、生产、销售和服务。为适应公司业务的快速增长,公司系统导入精益管理体系,为企业的持续快速发展打下基础 。 项目目标:
1、建立精益标杆线: 建立6S自主管理体系,试点生产线综合效率提升10%,精益物流配送改善,初期TPM管理体系构建 2、精益专项改善及人才培养认证:完成“精益绿带”课程培训,并完成体系8个质量改善专项,输出重大改善专项,基层干部基本掌握精益生产的应用,并培养干部晋升储备人才 项目执行:
1、精益班组以底盘中巴线和总装大巴线为试点,围绕七大任务,通过推动精益车间管理体系建设,实现现场管理过程标准化、规范化,输出标准化事项20余项,涵盖两条示范线8个班组,培养精益督导师8人。 2、完成6西格玛绿带全部35学时培训,培训理论考试平均成绩82分;培训工具20项,结合项目应用12项,其中9项为新工具。精益课题推进思路以DMAIC方法论为主,过程中运用到系统的改善工具,结构化的解决问题方法论让产业精益改善有了共同的语言。 3、通过示范线推行TPM,对两条示范线设备及四围合装开展初期清扫活动并通过评审,基本建立了自主维护体系(AM)及专业维护体系(PM)提升了示范设备的维护管理水平,健全了设备管理体制。 4、物流配送小组通过提高拆包上线率、减少二次搬运、精益货架的引进使用、成套配送及配送路径规划等措施,减少了线边空间占用,改善了现场6S。 5、生产效率提升通过对工序作业时间分析,车位人员作业布置的优化、瓶颈工位作业及工装器具的改善,转变观念由对外部的抱怨转向内部的改善。累计工效平均提升5.5%达成提升5%的指标(底盘提升9%,总装提升2.1%) 6、项目期内提案实施数翻倍达1049件增幅效益86.7万,达成指标。 项目成果:
1、专项指标得到一定的提升,并带来300多万的经济效益,现场6S改善得到明显的改善,示范线内建立起较科学的班组管理体系。 2、多维度多层次的人才得到培养:参与改善的一线员工、班长、专员、督导员、体系内基层干部及其它项目相关成员,这些人才将是后续持续改善的主要种子与核心力量。
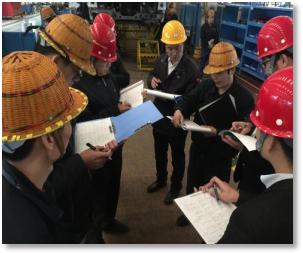
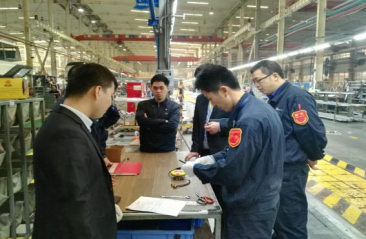
|