TPM推进过程的四大误区
TPM的核心是全员参与和以设备为中心,即以设备综合效率最大化为目标,建立涵盖设备、研发设计、生产、品质、HR全部门贯穿于设备生命周期的设备维护体制。从TPM的定义可以看出TPM的重要性,但在实际推进过程中TPM的推进难度要大于其他精益项目,主要原因是TPM不同于效率提升、布局设计、物流规划等典型项目,这些项目在结束后的主要工作是标准化并维持改善成果,而TPM一旦开始就相当于“增加”了员工日常工作,加之TPM见效期要长于其它项目,因此企业对TPM的认知普遍存在误区,特别是企业的高层,领导层在认为TPM是一件重要事情之前不会太重视TPM,因此在开始导入TPM管理前企业必须正确的认知TPM,调整高层的思维,而其中重要的一项内容就是规避以下在TPM推进过程中的常见误区:
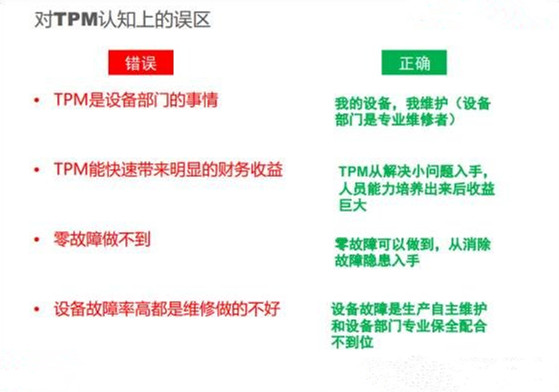
TPM是一个健全的体系,三个基本理念是预防哲学、零目标、全员参与。基于这三个基本理念,我们才可规避四大误区。
TPM是设备部门的事情
TPM是设备部门的事情的观点往往与“点检无用论”观点并存,认为点检工作不但增加了产线员工的工作量,而且对降低设备故障率并没有帮助。这种思维的错误之处在于没有认识到设备操作者点检技能的重要性,实施点检后故障率依然不降低是因为点检方法、技能没有达到要求。通过需制定较好的点检标准,并经过充分的练习,操作者才能掌握正确的点检技能。
点检的目的是让设备故障在很小的时候就能够被发现,把设备故障消除在萌芽阶段,所以点检是可以预防设备故障的,也就是说TPM不只是设备部门的事情,包括了生产线员工的日常点检,另外还有品质部的品质保全,行政部门与HR组织的保全教育培训,只有所有与设备相关部门的共同参与,才能做到真正的全面设备维护。
TPM能快速带来明显的财务收益
在推进TPM过程中要教导领导层认知TPM不会迅速带来财务收益, TPM在开始的时候,员工不会掌握很高的工作技巧,在能力增长的情况下,不断的从小处着手,才会带来很多的财务收益,这是一个量变到质变的过程。
零故障做不到
零故障是可以做到,设备故障符合冰山模型原理,把设备故障的产生的前提条件:如灰尘、松动、震动、锈蚀等问题全部解决,故障也就不复存在,从因果论来讲,穷尽并消除所有可能产生故障的原因和隐患,必然可以实现零故障。
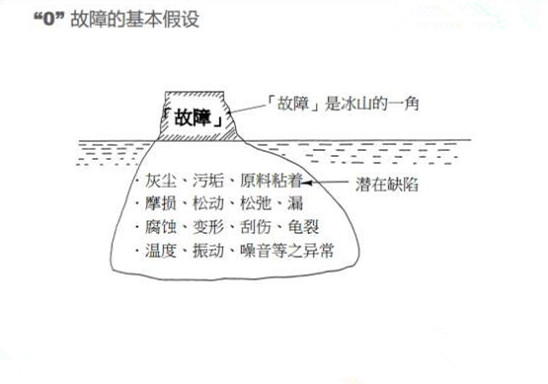
设备故障率高都是维修做的不好
设备保养是全员参与的事情,从设备的采购、使用、日常点检、维修、计划保全,是每个部门发挥作用的综合结果,而不是某个部门的事情。推进TPM后故障率依然很高是各个部门没有配合好,特别是自主保全和设备专业保全的配合推进,因此这种认知也是错误的。
只有规避错误的思维认知,才能让每一个部门认知到设备故障不仅仅是设备部门的事情,这样大家才有意愿和责任去参与TPM工作。
分享:冠卓咨询
说明:转载请注明“精益”