1.精益生产方式的特点
精益生产方式的突出特点是:追求生产现场的整体优化,各种现代化管理方法、手段紧紧围绕提高产品质量,增加企业经济效益进行配套设计,同步实施,以充分发挥其整体功能作用。这种生产方式一改传统的前工序推动后工序的“推动式”为后工序需要多少前工序供应多少的“拉动式”生产方式,其后工序是以市场需要为目标,组织整个企业进行准时化生产,它能对市场需求做出灵敏的反应。
这种生产方式能够最大限度地压缩企业的生产在制品的数量,减少资金积压,降低成本,提高产品市场竞争力,实现增加企业经济效益的目的。它把“超量生产”视为万恶之源,使工序间的在制品向“零”进军。这样可有效地加强生产现场在制品的管理,有利于保证产品质量,避免批量废品的产生,而且在劳动组织上实行一人多机操作。这种生产方式是不同于传统管理方式的全新的科学管理。它把以生产现场为中心,以生产工人为主体,以车间主任为首的生产现场管理体制和贯彻标准作业做为精益生产的基石,它要求一切生产后方部门都必须围绕精益生产提供准时服务,保证生产工人分分秒秒的不停地创造附加价值。
总之,精益生产方式具有不断求新务实,自我完善自我约束与制度控制相结合及充分发挥整体功能,同步化作业等显著特点。
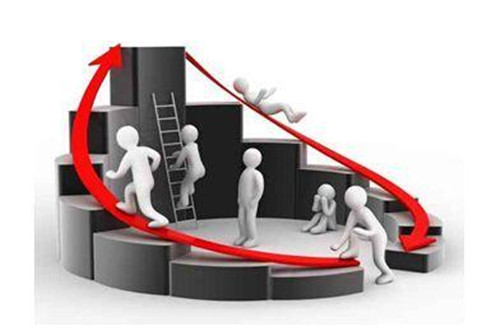
2.精益生产改造的组织实施
2.1.1 建全组织结构明确责权利
管理体制和组织机构是管理活动的框架和载体,管理活动的科学化有赖于组织结构的合理化。建立责权一致,结构合理,即有稳定性又有适应性的组织,确保其顺利运转,是完成精益生产改造任务的根本保证,也是落实建立现场管理体制指导思想的重要条件。精益生产方式对于设置企业内部管理体制和组织结构的要求是:总经理能宏观控制,基层组织能协同作业,生产计划服从于销售计划,销售计划服从于市场需求,有利于生产现场和企业管理整体优化,有利于贯彻标准作业,提高产品质量,降低成本,能增强基层组织协同作业的自觉性,有利于“以现场为中心,以生产工人为主体,以车间主任为首”的管理思想的实施。据此,公司应设立领导小组,在领导小组下根据不同项目、不同区域组成各种跨部门的多功能实施小组负责该项工作的具体实施。
2.1.2 做好各级人员的培训工作
精益生产方式是一项严密复杂的系统工程,它将多种管理技术和方法综合配套应用于现场,并强调发挥其整体功能作用,以最少的投入实现最大产出的一种生产方式,它与原来的生产方式相比较在管理观念、管理内容、管理方式方法上和企业追求的目标上都发生了根本变化。所以要想真正将此项工作做好,公司各级人员首先要更新观念,提高认识,改变在原管理基础上和客观环境里形成的根深蒂固的旧传统、旧意识。根据这些客观现实,企业可聘请专家,对各级人员分别进行培训,同时组织小组到有关企业进行现场考察交流,然后再结合所学理论知识进行讨论,制定出该项工作的基本原则及实施计划。
2.1.3 制定应遵循的基本原则
领导小组根据该生产方式的特点及本公司的实际情况并结合大家的讨论,制定出精益生产方式改造工作应遵循的基本原则。
(1)把提高“经济性”做为一切生产活动的落脚点。
(2)为了提高劳动生产率,必须坚持多机床操作,多工序管理的原则,工人的经济利益和人工作业率的多少相联系的原则。
(3)为了减少流动资金的占用,减少废品损失,减少无效劳动,降低成本,生产组织必须遵循工序间“一个流”,成本储备逐步下降的原则。
(4)为了适应市场需要,创造企业最大效益,生产准备工作和生产组织工作必须实行多品种混流生产的原则,如快速装夹工件、快速更换工装夹具、设备快速修理、快速换刀、快速准确地传递信息等。
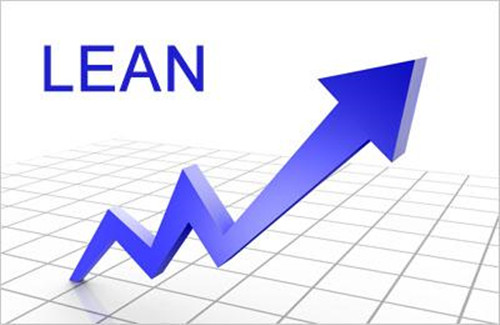
2.1.4 坚持以现场为中心,以质量为重点,顾客至上的原则
(1)坚持以现场为中心。生产现场的需要就是工作指令,所有单位都要全力以赴地为现场服务。
(2)坚持以质量为重点。把质量管理工作作为企业管理的重点事抓,把提高质量作为增强企业竞争力的主要手段,各项管理工作都要围绕产品质量开展,把产品质量作为评定各项管理工作的基本尺度。
(3)坚持顾客至上。后序是前序的顾客,前序的生产以后序的需要为标准,在质量上,坚持后序监督前序的原则,凡质量不合格不得往后序流转,如流转到后序,由造成质量问题的前序负责,如果本工序没有及时发现前工序出现的质量问题而继续加工,然后流转到后工序,后工序发现后,责任由本工序和出现问题的前工序共同承担。
车间是科室的顾客,科室的工作要围绕车间的需要进行,一方面为车间提供生产上必要的生产条件,另一方面,需急车间所急,想车间所想,为车间提供准时优质的服务,而且要把车间生产活动的效果做为评价科室工作好坏的依据。
2.1.5 坚持在实践中不断完善提高的原则
管理标准是企业各部门及个人行动的规范,是生产活动结果和工作质量评价的基准,它直接关系到企业生产经营活动的效果,它的科学性、合理性、准确性和先进性必须经过现场实际的检验来确认。制定标准时,不管查阅多少资料,很难从资料中全部了解现场的实际情况,必须要到现场中去进行验证,通过实践来纠正偏差、完善提高。当现场的客观条件和环境向更高的层次发展时,各项管理标准也要随之改变,并要到现场实践中去接受检验,使之更具有先进性、合理性和准确性。
(1)制定实施方案,明确分工,确保各项工作按计划实施。
精益生产方式的根本目的和最高原则就是降低成本,提高产品质量。各项工作都要从这一根本目的出发进行设计和实施。公司领导小组根据这一根本目的及要遵循的基本原则制定出该项工作的具体方案,并确定各项目负责人,使各项目分工明确,各负其责。
生产组织:在生产现场的管理中,坚持以生产现场为中心,以生产工人为主体,车间主任为首的指导思想。生产组织的核心内容是实现工序间的“一个流”生产,它是工厂管理水平的标志,是创造企业最大效益的主要手段,是工厂各项方法配套实施的一个重要内容,也是新旧管理方法争论的焦点。所谓“一个流”生产,是指生产线内部相邻上下工序之间流动的在制品数量,在任何时候不超过紧前工序的装夹数量,在运动状态上,不间断的、不超越的、不落地的运动过程,为此要求操作者,必须严格按节拍生产,严格执行工艺纪律,按标准操作卡进行操作。
(2)实行多机床操作,多工序管理,生产线的投入与产出工序由一人管理,其设备由一人操作,目的在于使生产线的投入与产出同步,同时也是为了充分利用生产工人的有效时间,创造更多的附加价值。以生产节拍为周期,以工人手工作业为中心进行多机作业组合,采用标准组合表的形式计算出一个周期内最大限度组合的工序数,机床台数,来确定一个操作者的作业单元(岗位)。
实施多机床操作的劳动组合前,首先要明确责任部门与实施范围,制定出劳动组合方案及各种标准作业指导书。其次还要做操作工人的思想工作,使工人了解多机床操作的意义,从一人一机的传统组织形式中解脱出来,做多机床操作的推行者和组织者。
(3)生产准备和设备管理
为了减少设备停机时间和降低工人的辅助劳动量,充分利用生产工人的有效时间,为生产工人最大限度地创造附加价值提供准时服务。为此在方案的设计中,最大限度地考虑到工件的快速装夹,刀具的快速更换,工人操作的最小位移等等。设备管理的宗旨是为生产提供准时服务,其任务是为精益生产方式提供必要的条件。因此,精益生产方式要求维修工人要服务到生产现场,及时掌握设备状态和设备隐患,有针对性地进行修理,使设备处于良好状态,为均衡化生产提供充分的必要条件,为达到此目的设备管理实行维修工人现场驻屯,走动服务,巡回检查,快速修理的管理方法。
(4)标准化作业管理严格执行标准作业是精益生产的一块基石,标准作业是指生产过程中的各种要素(人、机、料、法、环)最佳地组合起来,并以目视管理的形式,构成各自的作业标准进行操作,且符合作业标准要求的行为过程。精益生产作业标准包括生产节拍,工艺规程在制品定额和质量标准四个要素,它是指导作业人员正确操作的依据,也是管理人员在生产现场指导检查工作,及时准确地对生产过程中出现的问题进行原因分析和改进的行为规范,因此,应将制定的作业标准悬挂在现场作为作业人员的行为指南,在执行中发现不完善不合理的地方应及时加以修正和补充,按照一定程序制定新的作业标准。
总之,组织标准作业可以消除各种无效劳动和浪费,提高产品质量,为实现均衡生产奠定基础。
(5)质量管理精益生产对产品质量的稳定程度有较高的要求,需要较高水平的质量管理做保证。因此,我们必须要做到:
要把工序的概念从主体工序拓展到辅助工序和环节工序,增加为保证产品质量所必须的辅助工序和环节工序,使制造工艺更科学、完整、合理,更加有效地进行制造过程的质量控制,真正做到使质量控制在过程中。
要保证道道工序都合格,保证形成工序的诸因素项项合格。工序合格是生产合格产品的基础,工序不合格,产品质量就没有可靠的保证。
精益生产对人的素质提出较高的要求,人是产品质量形成过程中最活跃,起决定作用的因素,要生产出高质量的产品,对人的思想素质、技术素质和身体素质的要求也必然要高。
公司要有一个良好的运行有效的质量管理体系及满足要求的质量能力作保障。
3.总结验证
总结验证是每一工程不可缺少的一个阶段,在这个过程中我们要总结经验发现不足,最终达到持续改进的目的,真正使PDCA循环(计划、实施、验证、改进)应用到每一个过程中。实践证明,这种精益生产方式是我国现代企业充分挖掘企业素质及活力、提高市场竞争力的一大法宝。因此,愿她能在提高我国工业企业的生产现场管理水平,推进我国现有工业企业管理,加速我国企业管理现代化方面发挥出积极的贡献。
文章来自网络,版权归作者所有,如有侵权请联系删除