TPM管理,即“全员生产维修”。是一种全员参与的生产维修方式,主要是通过建立一个系统全员参与,使得设备性能达到最佳状态。那么,推行TPM管理有哪些要素呢?
一、TPM的基本推行工作做TPM一点不能急,一些步骤必须要遵守,否则就会前功尽弃。
第一步是培训。
在企业开展TPM管理工作的时候需要大量的TPM培训,给员工灌输TPM管理方面的知识,在前期开始前,以及实施中,都要不断地进行,里面除了涉及到一般的5S,七大浪费,QCC,QC七大手法外,还有MTBF,MTTR分析,动作分析,时间研究,工序分析等等,设备原理等等,还有好几十场不同内容的培训。
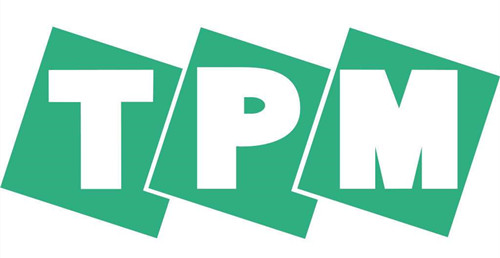
第二步是设备5S管理工作,在日本叫做经营直接型5S管理,或新5S。
设备5S管理就是要求:
整理:除了现在实施的整理内容外,它在设备上的内容还有:将闲置的设备直接拉走;对设备上的一些无用的,人工加上去的东西,立即清楚。将设备修理工具分开,维护工具分开,模具分开,都是按照一般的整理知识来做的。特别是设备上要用到的油,一定要按照需求量来准备,将多余的拿走。
整顿:对设备的很多地方需要做标示。那些地方要给油,频率如何;设备分为那些功能,分段标示;设备的消耗零件要标示;所有可能导致严重后果的开关要标示;工作区域和非工作区域要标示;设备易发故障部件要标示,等等。
清扫:让设备每个角落都干净,包括设备所处的场所;给设备定期管理注油,凡是需要有油的地方都要这样管理,让设备良好的转动。在一般工厂里,前两个S是重点,在TPM里,第三个S是重点。同样,5S管理是永恒不变的活动,也是企业推行TPM管理工作的基础工作。
第三步是总点检,设备的总点检查有很多内容,需要将设备的每个细节都做详细的分析,包括生命周期分析,故障可靠性分析,等等。 当然所有分析并不需要专业的统计,简单工具就可以了。然后做一个设备的总点检系统。在这里,需要培训点检的知识,包括设备的系统工程学,点检的要点,点检的要素,点检表的要求等等。
第四步是个别改善,怎么样调动一线员工的改善能力?
建议:
首先要培训一线员工的改善意识;你会发现很多工厂的员工对改善一点意识都没有,因为在他们眼里,连什么是改善都不知道,也许很多人会说他们工厂不会,但可以肯定的是,10家公司里,起码9家公司的一线员工对改善都没有好的意识。所以意识的培训,就很重要了。不要说员工,甚至很多专业的顾问,都对改善不理解,这里说的改善是Kaizen,而不是Improvement。二者是区别的。
其次要培训足够的改善知识,你面对的是一线员工,所以他们的知识都很肤浅,怎么给他们培训一些改善知识,需要很好的技巧。
最后改善欲望的调动,很多公司的员工都没有改善欲望,不管他们对公司满意与否,对于是否比一般工作多余部分的改善,没有动力。怎么调动他们的积极性,这是一个很重要的问题。
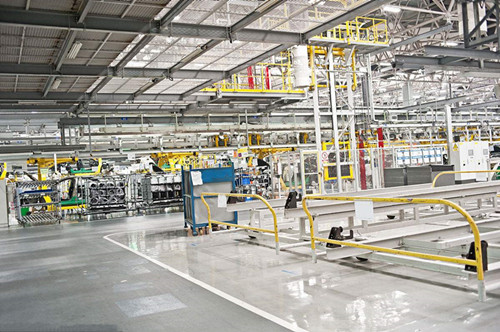
二、时刻记住TPM的结果是要什么,一些人的搞的TPM,到最后,是做的不错,但结果往往没有很好的体现。
究其原因,发现他们做到最后,往往是把TPM里面的三个结果要素的其中放到一边凉快去了。很多公司经常没把产品合格率搞好,是他们觉得这很难搞,而提高设备的时间效率和性能效率是否更有兴趣。这里,不妨采用TQM,把TQM的方式用到TPM的产品合格率上。特别对于一些非大型机械设备工厂,非常管用。
三、结合精益生产思想一起来在一些小型设备加工工厂。
很多人搞TPM,却只着重强调设备效率,忽略了精益生产的其他改善内容,这里如果大家在实施的时候,将精益生产思想随时做一个思考基础来进行,那么结果大不一样,比如,你是不是要采取Cell生产模式?你的价值流过程有不增加价值的地方吗?或许你还可以做一张VSM图。当思考这些后,你发现,很多时候,你可以改善设备效率以外的很多事情,而这些事情在工厂的以前,似乎是很难改变的,这个时候改变了,效率可能大大提高了。
四、注意TPM的八个支柱
很多时候,你会发现一些公司在做TPM的时候,往往做着做着就成了设备部和生产部的事情了,其他部门都好象无关了。这里建议大家在一开始的时候,发动TPM动员会的时候,就做一张详细的计划甘特图,将工作的详细计划做出来,越详细越好,如果不对,以后可以修改,这样就不会忽略了
五、注意新设备管理
在日本,设备投产,或者新产品投产的那段时间,一般叫做初期流动,其实汉语意思也能理解了,就是初期的流动嘛。在做TPM的时候,很多工厂,发现小型设备长,在这个过程会有设备购入,这些东西在TPM的实施期间很容易被忽视,反而是实施完后还不会。所以在实施TPM过程中,对设备管理的一些体系要正规建立成系统。还有,对新这个期间的新进设备要特别注意管理。因为大家都不希望做重复的事情。
文章来自网络,版权归作者所有,如有侵权请联系删除