近年来,越来越多的企业踏上了精益改善之旅,而这其中又不乏企业以5S改善作为精益的起点,但真正坚持下来并通过5S获得改善成果并顺利走上精益转型之路的企业却很少。因此,大家对于5S的看法都是众说纷纭。
在推进精益转型的过程中,我们往往会犯一些错误,诚如有时我们会把精益看得过于简单,有时又看得过于复杂。近来,在与很多客户交流5S持续改善的想法时给了我很大的启示,即在精益实践过程中我们需要不断Hansei(日语反省的意思)以真正掌握精益的原则、原理和方法,从而帮助我们即立足于本职工作又能有所收获。
面对5S改善无法在企业持续时,或许应该停下脚步反省下:我们推进5S这些改善方法和工具的真正目的是什么?我们在付出巨大努力推进5S后获得了什么?这些成果如何能在我们的企业维持下去?
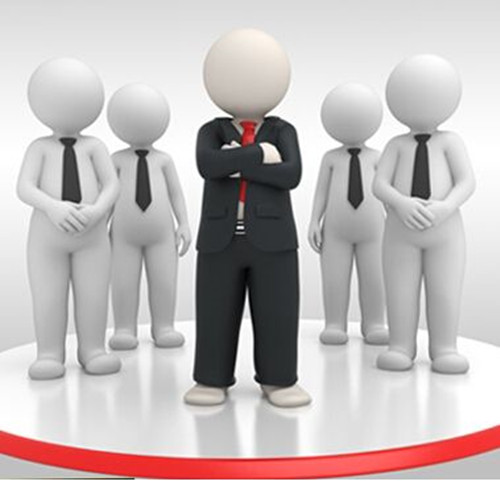
在此,我们不妨来追溯下5S的起源。5S来源于五个日语词汇的首字母,分别是SEIRI整理,SEITON整顿, SEISO清扫, SEIKETSU清洁, SHITSUKE素养。关于5S的实践最初是被当做一个体系应用于1950年代的日本制造业,当时他们正试图在漫长的生产流程中通过精准的标准作业,在满足节拍时间的前提下生产出具备完美质量的产品。在此背景下,5S改善的目的就是为了确保任何工作都得在节拍内高质量地完成,因此流程中的所有事物都得确保在正确的地方以避免产线员工在工作时“寻宝”,哪怕是花费1秒或2秒的时间。由此可见,精益工具、方法(5S也一样)的实践与应用通常是为了使我们的工作可以变得更简单、更好、更快并且更便宜。
回归我们的现场,企业推进5S的目的不尽相同;有倡导打造一流现场的,有为提高员工士气的,有为给客户和投资者留下深刻印象的,有为提升企业品牌形象的,或者是为了精益转型而轻松入门的,等等…以上这些的出发点都无可厚非,但就5S这一工具本身而言,其根本目的是使高效、良好的工作成为可能并可以持续下去。
基于这样的目的,如何使5S改善在我们的现场得以持续,或许首先我们应该回归到我们的工作,重新审视:我们的工作到底是什么?流程步骤是什么?如果在没有中断、没有时间去寻宝的要求下来完成每一步,目前已知的最佳方式是什么?每个步骤需要什么材料和设备,他们的标准位置是什么?5S能以何种形式帮助这些工作实现?以及需要通过什么样的严格审核?...我发现5S改善实践的本质是帮助我们审视并更严谨地进行工作设计,以便使我们的工作更具价值。
在精益改善的道路上,没有放之天下皆准的方法,丰田的TPS也是不断经过内部改良得以维持。通常就5S改善而言,原理和方法都是非常清楚的,但是如何让其在不同环境下生根发芽,就需要我们因地制宜,才能最大限度地持续发挥其作用。以下几点建议或许可以帮助我们更好地维持5S改善成果:
1. 深入理解工作
精益里面强调对于“好”与“坏”的认知,同样,在开展5S改善前,我们需要认知我们的工作是什么?每个工作岗位的目标是什么?这有利于帮助我们理解工作的价值在哪里,基于这样的价值我们的5S改善的目标就会很明确。
2. 鼓励员工体验
客户导向是精益的首要原则,在开展5S改善过程时,我们同样要以改善区域的员工为首要客户,他们的参与和体验才是创造最佳工作场所的途径。在辅导一个客户开展5S铜牌认证过程中,内部员工的参与和体验改变了整个项目的成果,现场员工在一次次尝试与改善过程中为现场带来了意想不到的变化,员工智源的开发需要构建渠道与试验场。
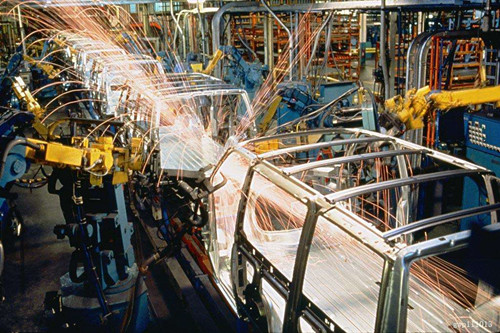
3. 聚力构建标准
没有标准就没有改善!而5S改善历程,标准的建立可以说是需要耗费大量人力物力的过程,许多企业的5S改善无法在工厂内部形成共识,往往是因为构建标准的过程过于漫长,导致人员和现场的变化无法很好地维持,改善完不久就回到了起点。聚集精力,快速改善,构建标准,在此基础上不断改善,改善成果的维持相对容易。
4. 系统协同反馈
系统的运行要求各环节的协同与反馈,5S改善亦是如此,不能把5S改善当做是一项单独的工作进行推进,试想1950年代的日本制造业,如果不是生产系统提出的要求,5S的推行力量就会变得单薄而不可持续。因此,我们在推行5S改善时要与企业的运营系统或是生产系统协同,基于系统的反馈才能不断提升。
文章来自网络,版权归作者所有,如有侵权请联系删除