1 六源知识基本认识
污染源_灰尘、油污、废料、加工材料屑等。
困难源_花时间的,不好做,不方便费力的操作。
故障源_造成故障的潜在因素.
缺陷源_会导致产品质量异常,不合格的因素。
浪费源_指任何不产生附加价值的事或物。
危险源_潜在的事故发生源。
2六源查找方法
1、“五觉”法
2、视、观、看
3、画圆站立法—丰田观察法
4、反复的清扫、红牌作战
六源的查找不是坐在办公室里面想出来,或者来个头脑风暴法讨论出来的,必须到现场去,观察现物,了解现实;唯一的方法就是通过反复的清扫及红牌作战找出发生源和困难源。
5、制作清单和分布图
6、辅助分析工具
目的:用科学工具进行彻底的改善。
认识“修理和修补”的真义方可进入改善方法掌握。
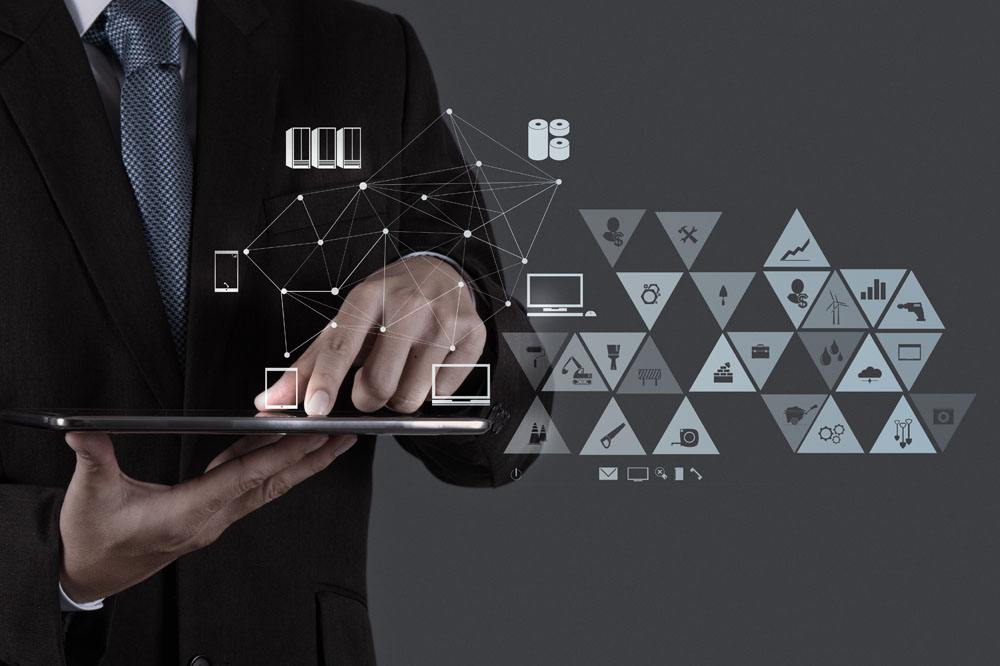
3 六源治理改善方法
1、困难源的治理方法
(1)难以清扫的改善方法(缩短清扫时间)
(2)难以注油的改善方法(缩短加油时间)
正确的加油方式是根据用途的不同,将干净的油从规定加油口,在规定的时间,只注入规定量的油。无论想要将加油时间缩短到多短,这些原则不能忽视:
①掌握加油部位,使加油变得容易
②统一油的种类,是加油变得容易
③准备好“油品站”,使加油变得容易
④将难以注油的注油口换个位置,使加油变得容易
⑤讨论“集中加油方式”或者“自动加油方式”,使加油变得容易
(3)难以点检的改善方法(缩短点检时间)
设备的点检部位到处都是,在“防护罩不看见的地方”、顶部等等,有时只能用“不自然的姿态“去点检,花费很长时间。那么要如何才能缩短点检时间?(点检高效化是保证员工完成点检任务的前提):
①让看不见的地方能够看得见,使点检变得容易
②以平视的高度、从设备前方开始点检,使点检变得容易
③让眼睛看不到的东西可视化,使点检变得容易
(4)难以操作的改善方法
车间的操作动作是影响效率的关键,操作困难会造成时间的浪费,也会导致员工感到疲惫,因此对操作的改善可以“立竿见影”,受到员工的认可:
①巧用工具,让操作更轻松
②统一紧固部件/同规格部件,让操作更轻松
③防止松动,减少操作频次(防松动装置)
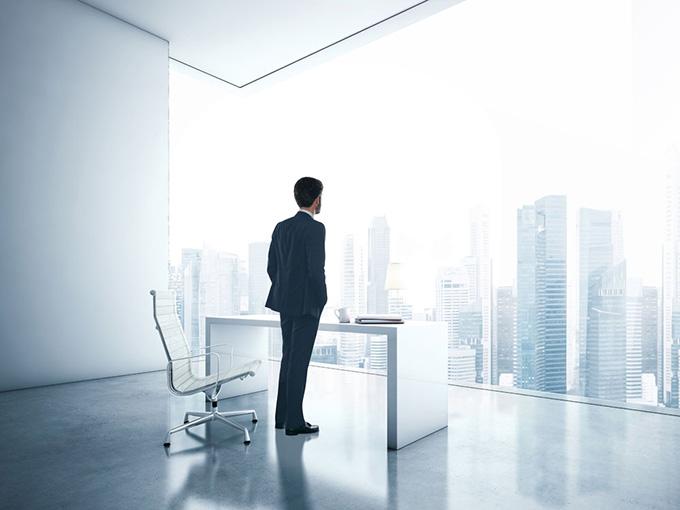
(5)难以调整的改善方法(缩短调整时间)
车间的调整/调试作业频繁,设备异常、维修复原时都会涉及到调整,如调整气压的大小、调整距离等;一般情况下,调整作业是靠个人的经验,用不断试错的过程达到最佳的调整位置,因此耗时比较长,调整都是浪费:
①采取刻度化的调整方法,保证一次性成功
②采取防错法调整方式,保证一次性成功
2、污染源的治理方法
(1)“切断”污染源的方法
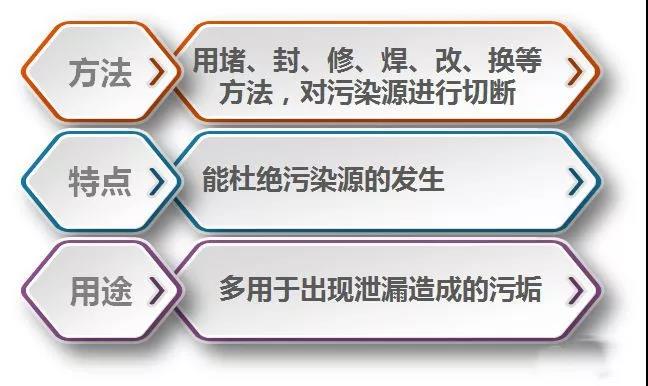
(2)“集中”污染源的方法
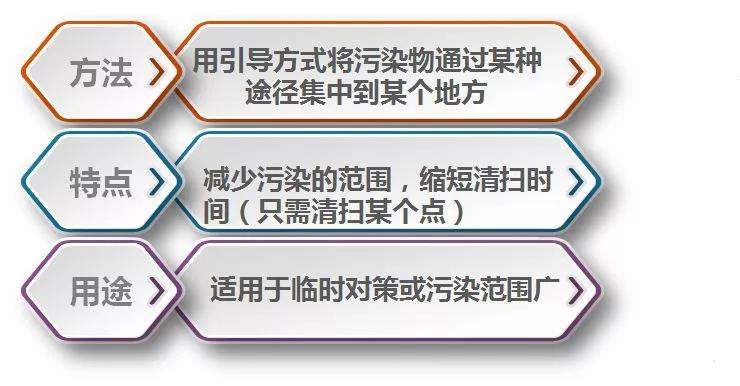
(3)“防飞溅”污染源的方法
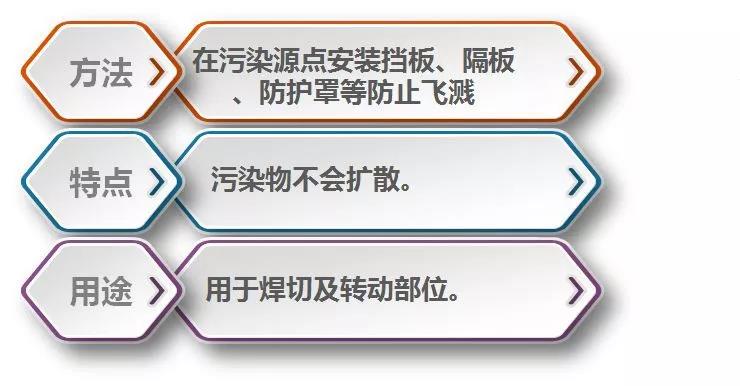
4六源治理激励方法
1、三大法宝的应用
(1)小组会议:定期组织小组成员对六源治理进行商讨、交流。
(2)OPL(知识点滴):将改善的亮点、高效的操作方法形成OPL。
(3)宣传栏:可利用 看板展示,让员工了解。
(4)网络(新增):利用内部网络平台,让小组成员更多的了解。
2、六源改善激励
(1)冠名激励
以作业者的姓名来命名,如:XXX工具,XXX操作法等。
(2)认同激励
在公布栏上创建“优秀员工”、 “改善标兵”、 “金点子状元”、“六源查找能手” 等栏位,图文并茂介绍优秀者。最优秀人员可以由厂长亲自颁奖,也可以获取跟厂长共进晚餐机会等。
(3)奖品激励
如提案奖。发有意义,或很适用的奖品给优秀者。
文章来自网络,版权归作者所有,如有侵权请联系删除
感谢冠卓咨询老师对项目组的全程辅导,通过做项目我们学会了如何用系统科学的方法分析研究问题;开阔了我们的视野并让我们的管理人员明白了团队协作的重要性。
——北京某电器公司