在20世纪初期,国内的制造企业还处于单件生产方式与大量生产方式并存的阶段。2010年之后,大陆人口红利消失、劳动力短缺、工资大涨,土地环境汇率等成本也大幅上扬,制造企业也因此进入了技术和商业模式的双重巨变期,希望在保证质量的同时寻求更低成本的生产方式。

然后任何一种生产方式的转变,都需要经历一段长时间的适应和磨合期。大多数大量生产方式厂家,都需要一个与之毗邻的精益竞争者,并且需要经历一种“创造性危机”才能有所变化。对许多发展中国家而言,精益生产是无需大量投资,便可以将生产制造技术迅速提高到世界级水平的一种手段。亿欧之前对精益生产这种生产方式的的基本理念和相关工具等做了一定的梳理,现在想要探讨在智能制造的时代背景下,精益生产能否在国内发挥应有的作用?
精益生产是智能制造的前提
精益生产又称精良生产,其中“精”代表精良、精准、精美;“益”代表利益、效益等等。精益对生产中的过度生产、等待、运输、过度加工、库存、缺陷返工、走动、人才浪费进行了聚焦,并提出了诸多的方法予以消除。精益生产的理念就是杜绝浪费任何一点材料、人力、时间、空间、能量和运输等资源,对由人、设备材料和信息等要素组成的工作系统进行整合、设计和改进、优化。
我们总会把当前企业使用的MES/ERP这种管理工具理解为数字化系统,但是,所谓的数字化运营的本质在于运营,数字只是实现的数字化运营的手段。之所以说精益是数字化的根基在于精益为生产提供了各种量化方法和工具,例如KPI、OEE、TPM、RCA、5S、目视化管理、看板等。这些量化方法和工具使得工厂得以被量化、可视化以及透明化,使其一切都服务于其经营目标:质量、成本与交付能力。
工程院院士谭建荣曾经表示:“精益生产和质量工程是智能制造的前提和基础。“他表示,如果生产是粗放型的,那就没办法搞智能制造,所以首先要精益生产,通过机器人技术、人工智能技术去实现精益生产。
当下国内对于智能制造的讨论多数聚焦于技术创新实现,标榜智能制造产线。另一方面,一些企业贪图政策红利,陷入了为了智造而智造的怪圈,大肆引进机器人,新系统,偏离了企业经营的本质。事实上,对于企业而言,如何厘清经营与智能制造两者的关系,建立持续有效的路径进行分析与预断,并逐次实施整体战略,尤为重要。
在机器人还未普及的时候,主要依靠人与物还有机械的配合,因此需要通过精益管理的方式让三者“啮合”。现在的智能工厂其实是在精益管理的基础之上延伸的,设想一下,如果一家工厂的管理理念非常落后,制造水平很低,想要单纯通过增加机器人和自动化设备就实现智能制造,实属异想天开。
事实上,真正应用精益生产的工厂(俗称精益工厂)有两个关键的组织特点,一方面它能够把最大量的工作任务和责任转移到真正为做增值工作的工人身上;另一方面有整个车间将设置有处于适当位置的检测缺陷系统,一旦发现问题,能快速追查并找到问题出现的最终原因。这意味着生产线上的工人间采用的是团队工作的方法,并且车间应设有简单而综合性的信息显示系统,它能让工厂线上的每一个人对问题作出快速反应,并全面了解工厂的情况。
精益生产并非一剂一吃就灵的神药
精益生产并不是一剂一吃就灵的神药,正如妄图用三个月时间啃下高三学子饱读三年时间所积累的知识一样,国内某些企业生吞照搬的做法只会消化不良。
目前,我国的市场情况与丰田公司在提出精益生产方式时所面临的市场情况是非常相似的,随着市场日益成熟,竞争越来越激烈,企业面临各种挑战,而企业的生产技术水平低,资源资金短缺,尤其2018年是资本寒冬的一年。
此外,我国企业在生产制造方式上存在极大的缺陷,主要以高能源损耗、过度依赖劳动力的粗放型管理方式来获得企业的增长,效率低下的同时导致企业增长缓慢。目前大部分的制造企业处于产业链的中下端,从生产过程来看,属于粗放型的、简单型的、加工型的生产方式。为了使我国制造型企业从竞争中胜出,提高企业的经济效益,在我国企业中进行深入学习和推广精益生产方式,改进企业的管理方式、手段、工具是非常必要的。
总结一下,精益生产方式是“舶来品”,需要“国产化”。精益生产说到底是一种生产管理的理念。生产管理的主题是人。与日本倡导终身职业不同,国内的制造企业需要根据自己企业的情况和企业文化,步步为营地进行实施。
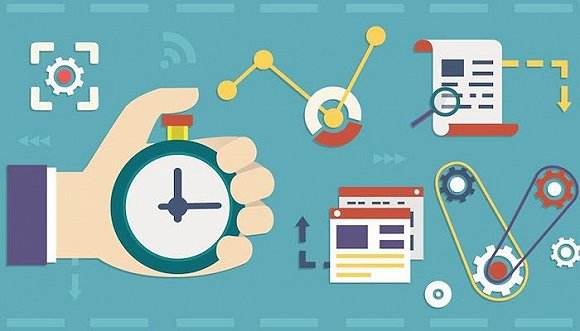
中国许多情况与国外不尽相同,所以在国外成功实施的生产方式对我国企业不一定适用。目前国内做的好的企业有海尔、联想、TCL、华为、格力和比亚迪等,其他制造企业也可以从这些企业中寻找适用于自身的经验。
文章来自网络,版权归作者所有,如有侵权请联系删除
感谢冠卓咨询老师对项目组的全程辅导,通过做项目我们学会了如何用系统科学的方法分析研究问题;开阔了我们的视野并让我们的管理人员明白了团队协作的重要性。
——北京某电器公司