TZ设备管理:
当前,我们在设备购置与验收时,重在考虑设备的工艺性能否达到产品的要求,对较为明显的安装、配置等问题也可及时判定出来,但很难发现设备隐藏的不靠性问题,虽然厂商有保修期一年的承诺,但”一年“其实无多大意义,有的在一年内就出现故障,厂商来修,而一年很快就过去了;有的刚过一年就故障频繁发生,这都给生产与设备管理带来很大的麻烦。故在此求教:如何在购置与验收时就能清楚地判定设备的可靠性与维修性?有哪些评价方法或指标?除了依照价格来判定外。
秀蕴知:
在购入过程中就考虑可靠性和维修性是很有益处的,但是也是需要长期有意识积累才能形成的,有很多优秀的企业有企业内部标准,比如按钮的尺寸,按钮的型号等都进行统一规定,写入采购规格书,这样对制造企业可能就有点非标,但是对本企业来讲,就统一了,后期备件库存资金、修复作业标准化等都变得很简单有效。另外就是会在购买合同中明确停工指标,乙方会有达成目标的方案,甲方对系统进行判断,看是否能够达成设定的可靠性目标,这个就有点像失效分析或者产品的FMEA,也是比较有效的。还有个典型案例就是飞机购买合同,MSG-3就规定了飞机可靠性的一系列指标,用于在购买时进行评估,总之,这块工作国内开展的好像不多,想做的话,单凭基层是不够的,需要企业的高层有这种意识.
罗先生:
评价标准——没有!小平同志说了:摸着石头过河。这个是双方都存在的风险。厂家不希望设备出现问题,影响企业形象!处理方法:
一、首先自己要熟悉机械设备原理(包括电器工作原理),可以事先发现设计问题(重点中的重点);
二、对于工作条件较为恶劣的部件,首先要选取质量好的部件;
三、横向对比,相同的设备对比,如果其他设备不出现的问题,这台出了,可以此理由向厂家索赔;
四、合同签订时,重点对于工作环境恶劣的部件、怀疑存在问题的部件做特殊说明(自己在使用中做好保养检测记录,作为厂家索赔的依据或着延长保修期的依据);
五、尽量和厂家搞好关系,一般能处理的问题,自己处理(首先要征求厂家意见和指导方法处理,)厂家也怕上门处理,费用吃不消,你处理了,省了厂家的费用,封住了他的嘴。
六、吹牛——告诉厂家,你们生产需要,会大量上此种设备。
以上几点,供参考!
我手上处理了好多这样的案子:自动抛光机——纯新设备,国内国外都没有,国人自己研发,推广时都说会存在这样那样的问题,那我就合同注明:某某机构几年内出现结构问题,免费更换。某某配件需要增配;然后,只要出现问题,电话联系厂家,指导我们自己处理(文字档案一定要留)。吹牛——这个设备越来越好,我们会大量上的。这样,3年了,厂家还在帮助处理,超出预期。
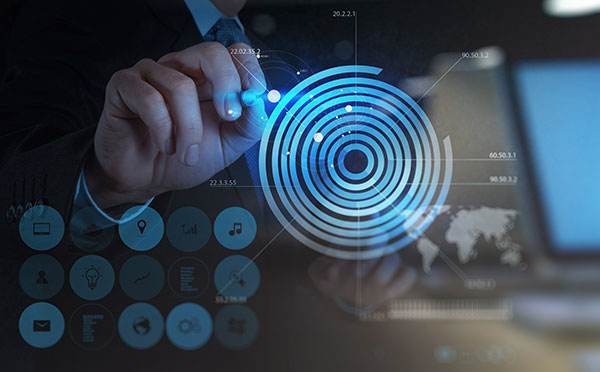
colwang:
评价可靠性、维修性有两个方面:一个是设备品质,一个是服务保障。对设备的品质方面主要采取零件分析和加工方式,比如钢材采用什么号牌的,零件是哪个厂商哪个型号的,特别是主要零部件,以及生产工厂的质量管理。
服务保障主要考察生产工厂或供应商的零件备货和服务团队,比如在本地是否有零件仓库或总仓调货是否及时,本地是否有维修服务人员或是否有专业的售后服务团队,技术水平如何,如何保证。
一般采用几个供应商及产品对比的方式来衡量。如果自己有基本标准,比如连续产能、疲劳误差等,一般属于初选的入围条件。对比主要是寻找最合适的,或在性价比中找到最平衡的一个。最后还可以竞标,但竞标比较专业,而且起标人要先有自己比较完整的要求。
关键是采购方要什么?这点很关键,性能越好价格越高,附加性能越多价格也越高。比如最近我见到有自我诊断功能的自动售货机,发生故障后它会自我诊断,连接网线或无线网后甚至可以自动发送故障说明给服务中心。机器还会自动每天发进销存信息给管理公司,可价格高的吓死人,厂家也只敢说是概念机。如果机器不能自我诊断,就要靠人来维修,那就是服务保障。是花钱买自动化还是花钱买服务,其实才是最困扰的问题,而且有的自动化反而服务还更重要。
而且保障是一个系统工程,机器进来之后的培训、工厂机修工的指导等,还包括常用零件、工具等,都是有成本的。有些厂家会以附加服务的方式另收费用。呵呵,说了一圈又回到钱上面了,采购很多时候考虑的不是东西好不好,而是需不需要。
xulijieyh:
非常赞同以上各位的意见,我想介绍给大家的是可靠性量化的计算的方法:即计算设备的能力指数Cmk, 当Cmk 》1.33时,设备才予以接收。这个指数是从工程能力指数演变过来。
在六西格玛的学习中可以找到,大家不防问问六西格玛黑带。
惩恶扬善:
问题是,CMK的数据从哪里来?谁提供?用户不可能为了买一台某种设备而去专门做这个数据的,而我们的生产制造商,谁家会有?又会有谁家愿意提供?愿意提供的厂家又有谁会保证他的数据真实可靠?
——如果用于评价可靠性的数据本身不可靠,这可是大笑话啦,哈哈!
colwang:
同意!
数据只有对比才有意义。其实在设备对比或厂家保障分析中,很多都是用数据对比的。没有数字的可以设定成数字,比如把优、良、中、差改成5、4、3、2、1等,都是很常用的。还有界定值的依据是什么?凭什么是1.33而不是1.34呢?
有数据就一定有误差,采购设备也没必要搞得那么标准,还是那句话,关键是需不需要。比如说,我这次对采购的设备的耐用性要求高,其它都无所谓,有两个厂商的设备,一个什么都好,就是耐用性差,另一个都很一般,但耐用性比较好。如果是我,就会把这次的采购标准中的耐用性分值提高,而如果用标准方式可能采购的就是那个耐用性差的。但可能下次采购的设备要求又变了,可能是多功能啦或是安装简便。如果采用标准数据判断,可能你每次买的都是不需要的,但都是最好的,呵呵,你怎么办?
这个学科其实很有用,比如十年前我陪我叔叔去买冰箱。有三款他看中了,牌子我不说了,但价格都一样:一个的蒸发盘管是一整根弯出来,但其它功能简单,外国品牌国内组装的;一个是焊接的,功能很多,国内品牌的;一个是采用新的卡口技术连接盘管,带省电功能,纯进口的。我最后推荐给叔叔的是一整根盘管的那个,同时我姑妈也买了,是那台纯进口的。前年我姑妈的那台买了,因为坏了,漏冷媒,还没办法修,一体成型的外壳,开不了壳。我叔叔的到现在还在用。道理很简单,再怎么先进的防漏连接技术,也比不上一整根盘管。而且不漏冷媒的冰箱更省电!用的时间越长越省电,当然是对比下来的,呵呵!

qqyyqq:
既然设备已经由厂家生产和销售了,至少对于设备本身来说,应该符合有关的国家、部委等标准。另外,就算是非标的设备,厂家也会有相应的测试手段去验证,非标的一般都有他们自己的专利、专有技术,我们是不可能得到那么深入的数据的。
研究设备的可靠性,一般是国防、能源、大型的钢铁、化工、电力行业,换句话说,在这些部门里,不掌握设备或零件的可靠性,会死人的。我们一般意义上的设备也不会涉及这么严重的后果,或者说,设备生产商已经考虑了必要的安全问题。
对于我们的设备,去研究可靠性,就像我们到菜馆点一个炒鸡蛋,我们只需要品尝鸡蛋做的好不好,再进一步了解厨师是怎样做出来的,也就够了。没有必要研究到底是先有鸡还是先有蛋这种问题!
如果一个设备运行一年没有什么较大的故障,应该说该设备就是满足设计和使用的要求的。
绝大多数的新设备出现故障的主要原因在于,相关人员对设备的原理没有较深入的了解,对设备的日常维护工作不足,甚至错误的使用和操作。
个人认为,处理好新设备新机运行后的正确使用操作、合理的维护保养和操作人员与维修人员的培训更为重要。
86605:
买设备时老板、财务最看重的价钱,希望越便宜越好,生产厂家开价100万的老板会还价40万。作为设备部门当然是希望设备越可靠越好,这样自己就不用经常维修,不用给使用部门投诉。但作主的往往是老板,所以只能买最便宜的,否则老板就会认为采购者有问题。
正常来说购买设备第一是要能满足生产、工艺的需要。第二是性能可靠、少出故障。第三就是功能先进,自动化程度高。第四才是价格要便宜。具体还是要看企业购买设备的实际需要。一般来说还是选用有一定规模和生产历史的设备厂家,从厂家的生产设备、加工工艺、选用的配件品牌等可以大概判断出设备是否可靠。
惩恶扬善:
在老板看来,省钱是王道。对一个不懂设备可靠性维修性问题的老板来说,价格是最重考量。
正如我们弄不清有机蔬菜与普通蔬菜的区别时,为尽量减少上当受骗的损失,就采买普通价格的蔬菜一样。
文章来自网络,版权归作者所有,如有侵权请联系删除
“感谢冠卓咨询老师对项目组的全程辅导,通过做项目我们学会了如何用系统科学的方法分析研究问题;开阔了我们的视野并让我们的管理人员明白了团队协作的重要性。”
———北京某公司总经理 苏先生