生产现场管理改善
2010年前,我们公司随处可以看到治具、工具凌乱摆放,机器设备布满灰尘无责任人管理,原材料、半成品、在制品、成品、不良品、包材摆放杂乱无章,状态不明,车间通道人车不分,经常出现工伤事故;作业区、物流区、办公区未明确规划且无标识,工人衣着不整,士气低落,浪费现象随处可见,这些问题已属公司管理中的疑难杂症。
为了解决这些疑难杂症,改善员工的工作环境,提高生产效率,提升产品的品质以及服务水平,减少浪费,此时公司领导引入冠卓咨询公司协助现场管理,建立工厂运营管理体系。
冠卓老师到我们公司走访现场之后,针对我公司制定一套系统的推进“5S方案”,首先给我们公司的全员培训5S相关知识,让我们对5S的起源与发展以及推进5S的作用有了初步的了解。 “人造环境,环境育人”,踏入新世纪,企业之间的竞争出现全方位,全球化,企业在强调以品质为中心的同时,逐步意识到以人为本的重要性。通过创造好的环境,培养和吸引一流的人才,缔造一流的企业,制造一流的产品,它精辟的概括了5S管理的真谛。
5S源于日本,其具体含义是指在现场中对人员、机器、材料、方法、环境等生产要素进行有效的管理,这是日本企业独特的管理方法,也是一切现场管理的基础,随后冠卓咨询公司制定了一系列详细5S推行计划,每项工作严格按计划实施。
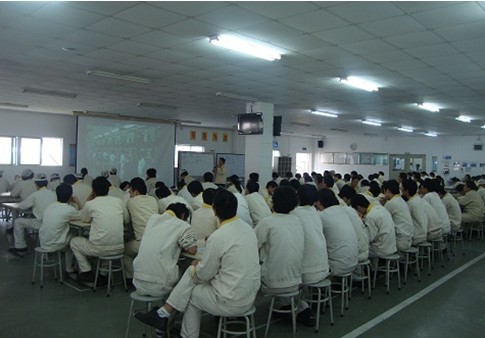
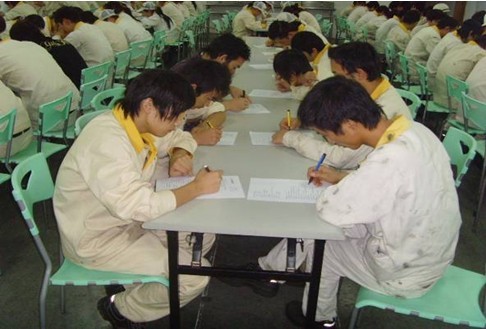
在冠卓老师的指导下,我们开展了:红牌作战、定点摄影、物品三定、区域规划、班组长定时自检互查,以及现场管理人员自发的5S改善创新提案活动。通过为期半年多的活动开展,使公司面貌焕然一新,大家的素养也有了很大的提升,乱扔东西的习惯没有了,严格按规划的人行道行走,真正做到事事有人管,人人有责任。
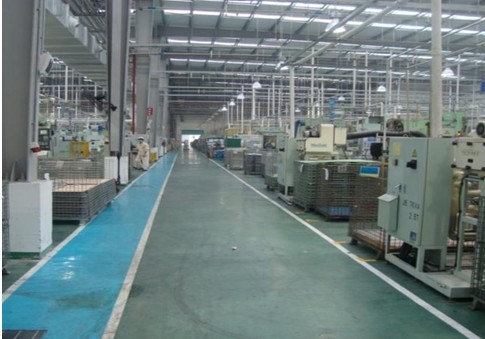
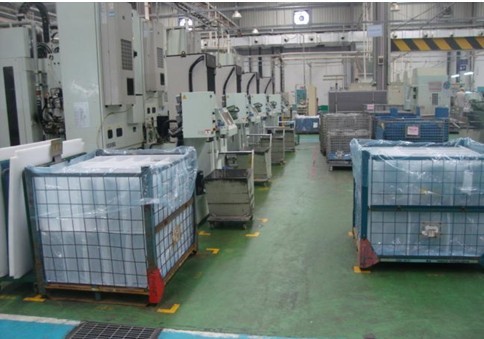
接下来是员工岗位培训体系建立及KPI量化考核体系,冠卓老师通过一系列的培训与辅导,引导全员认知建立员工培训体系的必要性及对生产、品质及公司运营等方面的影响。老师带领大家先梳理各部门工作职责、工位划分清楚,再根据每个员工的实际工作内容,运用科学、合理的评分方式对各工位进行岗位分级,在冠卓老师的指导下分别编制了公司的《通用知识》教材及各部门的岗位培训教材,大大的缩短了新员工及调岗员工的培训时间,各部门多能功覆盖率达到40%以上 ,L员工占比达60%以上,U员工占比达15%以上。

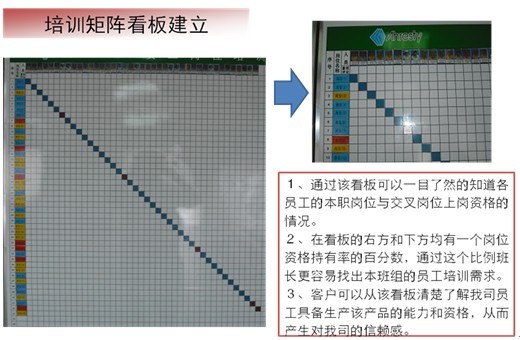
KPI绩效管理体系,首先老师指导大家如何建立绩效考核指标,再结合员工效率、质量、5S、安全、执行力五个维度进行评价,每天由班组长对组员进行打分,下班后记录在葡萄图上,作为员工当天的绩效,按2、7、1原则计算当月员工绩效。
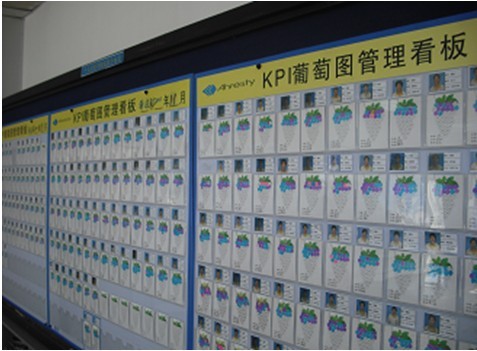
通过冠卓老师三年的时间辅导,管理人员能力得到大幅提升,公司也得到很大的发展,由原来的300多人工厂,发展到现在的1650人,原来一家工厂,现在发展到五家工厂(现 还在新建工厂),客户由原来的铃木汽车,发展到丰田、本田、加特可、CHAM、奥迪、日产、三棱汽车等,成为具有世界级汽车产品供应商。
阿雷斯提项目组长杨部长对项目评价:09年,面对着公司规模不断扩张而公司管理缺乏系统性、专业性,中基层管理人员严重不足的情况,公司选择了北京冠卓咨询公司协助进行工厂运营管理体系改善项目,并专门成立了改善组。经过摸底调查,确立了09~12三年改善战略。通过几期有计划的改善过程,冠卓为公司提供并实践了一套完整、系统、逻辑严谨的工厂运营管理体系,通过TWI、5S、生产员工岗位培训体系、KPI量化考核体系、TPM等一系列的现场改善项目,一线管理者能力提升、现场的面貌焕然一新,一线员工得以快速培训上岗,员工考核系统公平、可视,同时也培养了100多位从科长到基层班长的中坚管理人才。大家都公认改善组为“黄埔军校“,进改善组学习不仅可以学到先进的管理知识和技能,而且还助于职位的提升。
管理改善,冠卓的价值不仅仅在于提供现场诊断、改善建议以及课程辅导,更主要的是他能够成为公司改善团队的一员,和现场人员一起面对现场的问题和挑战,通过有效的方法指导,大大提升一线管理人员解决问题的能力、员工敬业度、现场管理目视化等,在这一过程中为公司培养出现场管理精英,为公司的发展打下坚实的基础。
对于我个人来说,是冠卓协助我实现了从技术到管理层面的华丽转身,不仅丰富了我的阅历、知识、技能,同时也通过这样的一次合作,使我的职业生涯发展更上了一个台阶。
编辑:冠卓咨询
声明:制造中国文章---属冠卓咨询内部专家原创内容,代表个人观点,授权于冠卓咨询网站使用;如需转载请保留原意并注明来源:冠卓咨询。请尊重原创!