首先来讨论一下现场的质量问题的分类:
按照质量问题发生的流程,问题可以分为:原材料质量问题、制程质量问题、物流质量问题、以及客户投诉的质量问题等;
按照质量问题的缺陷类别又可以分为:划伤、凹坑、脏污、等等产品外观性的问题,还有漏电、噪音、口感等性能类的问题;
不同的产品,不同的流程会面临不同的问题,所以质量问题的分类千差万别,包罗万象,如果用指标变化的趋势情况来衡量问题无非离不开以下三类典型的形态:
(1)因“突然不明原因”使表现与预期标准有偏差
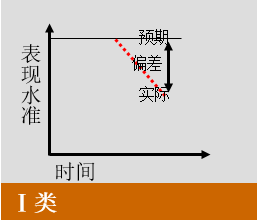

第一类问题我们把它称为异常性的问题。我们以某一线体为例,假设这个线体的产品的类型变化不大,取其线体的不良率作为衡量该线体的质量问题,第一类问题呈现的特征是平时比较稳定,假设平均差不多为0.5%左右,但是某一天或某一时刻,因“突然不明原因”使表现与预期标准有较大偏差,达到了5%。这类问题在企业里我们又称之为“批量”、或者“质量事故”;如果这个异常情况经常发生,比如每个月都有那么几次的话,那我们就得思考一下,流程存在哪些“关键控制点的缺失”?
解决方案:系统的梳理流程的关键控制点,并制定相应的管控措施
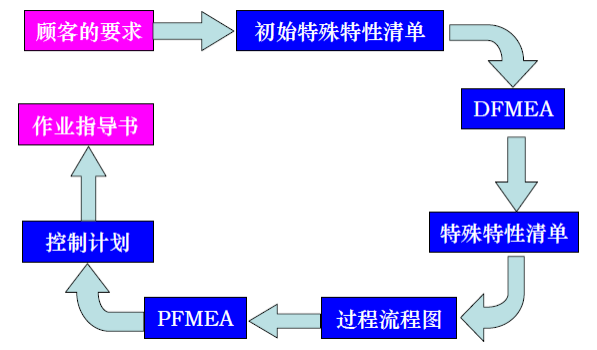
首选从客户的需求出发,识别客户的需求,然后形成初始的产品特性的清单,再围绕产品的特性清单进行设计端的失效模式及影响的分析,也是我们俗称的DFMEA,通过DFMEA的风险系数抉择特殊的特性清单,结合生产的工艺流程识别影响产品结果的过程因素,然后进行过程的失效模式及影响分析,也及时我们俗称的PFMEA,然后根据PFMEA的风险系数选择关键的控制特性纳入控制计划,最后就是控制计划里面控制的在现场落地实施。
(2)系统及流程一直未能达到的预期或者目标的水准
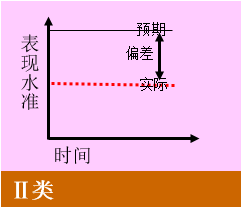
第二类问题的趋势特征比较稳定,用统计专业术语来描述就是波动比较小,但是稳定又分为两类:一类叫稳定的好(过程能力充足),另一类叫稳定的差(过程能力不足),如流程的合格率都维持的95%左右,也很稳定,但是就是没有达到我们的98%的目标要求。
解决方案:针对这类问题,我们应该更多的去思考:产品设计的问题、设备精度的问题、材料特性的问题、工艺参数设置的问题,避免往人员的作业手法去寻找解决方案。
(3)过程的平均值没有问题,但是过程波动太大
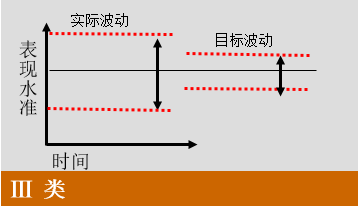

第三类问题的特征是过程的指标波动比较大,也就是过程非常不稳定。
解决方案:如果是第三类的问题我们应该更多去思考管理方面的原因,如果要把管理这个概念再细化的话,那无非离不开以下两方面:
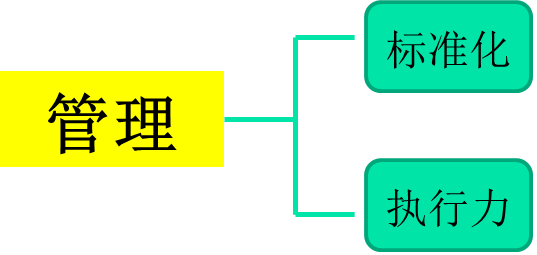
1.标准化:过程的作业手法、工艺参数、来料批次的检验标准等是否都有标准;
2.如果有的话,那就是执行层面的问题,涉及执行层面的问题又回到员工绩效考核的内容;如果现场的指标呈现的是波动比较大的情况,那就先做好这两个方面的内容,要不你做了关于流程优化的措施,如:优化的参数设置最后都会被抹灭掉。
总结:
用简单的趋势图就可以识别现场质量问题的现况,以便我们宏观的把握后续解决质量问题的方向,快速的切入问题的重点避免围绕问题进行笼统的人机料法环等方面进行分析验证。
本文为冠卓咨询原创文字作品,任何人或组织不得对本文进行篡改,转载或以盈利为目的行为,一经发现,将负法律责任。