2004年雅典奥运会男子110米栏,田径运动员刘翔以12.91秒平了由英国名将杰克逊保持了11年的世界纪录,获得了中国男选手在奥运会上夺得的第一枚田径金牌。因为刘翔,也因为精益管理咨询的职业工作,在2008年的北京奥运会,我忽然发现一个现象:高而瘦是每一个跨栏选手的基本特征,无不例外。经过大致的数据分析,是否可以得出一个结论:要想跑的快,瘦是必要条件?虽不能完全考究,却无人否定。由此联想到精益生产Lean Production的中文翻译,恰恰Lean在英语中的意思是瘦的、瘦肉,这个巧合让这个单词有点传神之译,可见一家企业想在竞争中以速度致胜,就要精瘦无负担,才能赢在前面。
"The Machine That Changed The World",最早见于1990年,作者詹姆斯•p•沃麦克(美)、丹尼尔•T•琼斯(英)和丹尼尔•鲁斯(美),中译名《改变世界的机器》,这本书由包括三位作者在内的多位MIT麻省理工学院学者用了近5年的时间对90多家汽车厂商进行对比分析后出版。在这本后来成为世界精益的伟大书籍,以汽车工业为例,第一次把丰田生产方式定名为Lean Production精益生产。再后来,作者又出版了续篇Lean Thinking(《精益思想》),进一步从理论的高度归纳了精益生产中所包含的新的治理思维,促使企业重新思考企业流程、消灭浪费和创造价值,由此标志着精益生产方式由经验变成为理论,一种新的生产方式诞生。
TPS创始人大野耐一曾说:“所有我们做的,就是不断压缩从客户下单的那一刻起,直到我们收到货款所用的时间。我们通过减少无附加价值的浪费,缩短时间。”这就是丰田人对精益的理解,也是基于此拥有强大的持续改善系统。
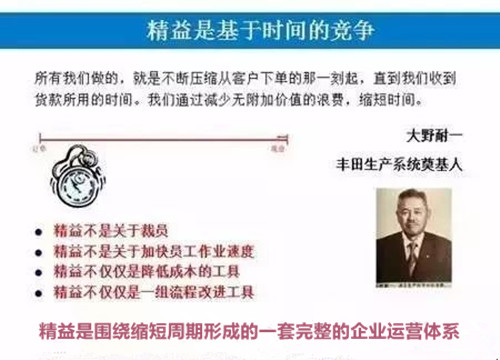
我从精益的角度看,制造企业的业务类型纵然千差万别,但都存在四大流程之中:
1. 新产品开发管理全流程;
2. 从概念设计到正式投产;
3. 从原材料采购到出货交付;
4. 从接受订单到到准时交付。
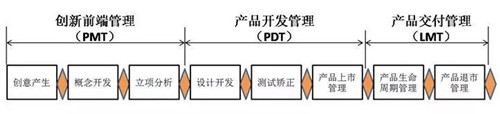
总体而言,从价值链分析实施精益生产的关键,就是分析这四大流程,在流程中消灭属于自己公司的“浪费”,目标是使无浪费和不增值的流程以最快的速度活动,其出发点是“以顾客为中心”,从顾客的立场观察产品在整个制造流程中获得的价值或者服务。换句话说,以缩短周期为根本目的,以消除浪费为实现途径,这也是价值流管理区别于传统改善的思维。这个精益周期派观点也是我一位多年好友精益专家刘宝生的一直秉承。
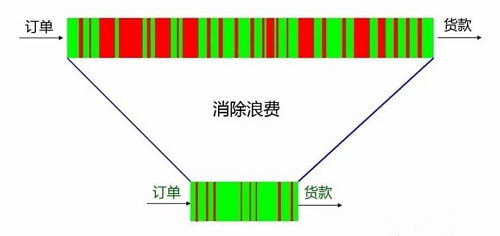
我们大体知道,从事制造产业和运营管理,有三大共性KPI:Q(Quality品质)、C(Cost成本)、D(Delivery交期),当然还有S(Safety安全)等。
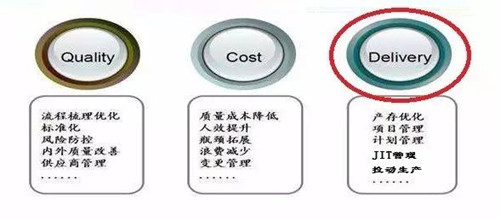
本文说的是通过精益生产主要解决“交货期”这一指标,如何通过削减库存压缩生产周期,从而快递提升企业的OTD。交货期通常由三部分组成:一是物料采购,二是生产制造,三是物流运输。关于生产制造周期,一直都存在一个很大误解,相当一部份人以为生产周期只和生产能力有关,想压缩生产周期,就要增加产能。但实际上,影响生产周期的因素有很多:原料库存、在制品库存、成品库存、生产能力、批量大小、生产顺序、计划排程。其中,库存是影响生产周期最大的因素,因此在丰田,库存被列为“万恶之源”,实施精益生产的企业往往把压缩库存作为首要追求,而这让很多企业老板难以理解,但其实压缩库存就能缩短交期、提高流动资金周转速度。
诸多美企、日企争相压缩库存的用意就在于此,譬如PC生产制造商,DELL公司就是一个典型例子。戴尔采用网络直销的办法,用户在网上配置自己喜欢的电脑,在一周之内,用户就能收到符合自己心意的的电脑。在短短几年内,这种销售模式帮助戴尔实现了世界销量第一的梦想,而支撑因素之一,就是其生产工厂能够在七天之内把顾客的产品生产出来并交到客户手中。
这样说来,企业完全可以利用产品流速去获得竞争优势(或者去弥补成本无法受控的上涨),这也就有了题目的观点:精益是基于时间的竞争。企业要想提升竞争力和盈利能力,从而在行业竞争中以速度致胜,就需要向刘翔那样,重在打造持续改善系统,成为Lean Enterprise精益企业,才能跑在时间的前面,跑在行业领先。
文章来自网络,版权归作者所有,如有侵权请联系删除