丰田生产方式闻名于世界,它不是对泰勒科学管理方式的照搬,而是加以改善创新,逐步形成自身独特的一套管理模式,丰田标准化作业才用了网络化、有弹力与创新的制度。
现代的社会环境与市场环境是,客户需求的变化越来越快,一线员工流动率越来越高,人工成本不断升高,动态用工和结构性用工成为必然。因此,现代企业必须保持高质量、高效率、低成本和快速应变的竞争优势,才能在竞争中生存下来。标准化管理是应对市场新情况的最有效力式。
所谓标准化是指,为了实现整个工作过程的协调运行、提高工作效率,而对作业的质量、数量、时间、程序、方法等制定统一规定,做出统一标准,也就是对人所从事的工作标准化。
作业标准化、标准化作业、变化点管理和改善优化是标准化作业管理的动态循环。日本和美国的企业实践证明:作业标准化做得越好,对员工技能的依赖越低,新员工上手就越快;标准化作业做得越好,生产人员越有条件进行变化点管理,一线干部越有时间推进改善优化;不断改善和优化的结果,是使企业作业标准化体系不断完善并得到动态维护。所以,“铁打的营盘流水的兵”,日本和美国在华企业甚至能用高达40%以上的季节性用工,还能保持强势的市场竞争力,标准化作业管理功不可没。
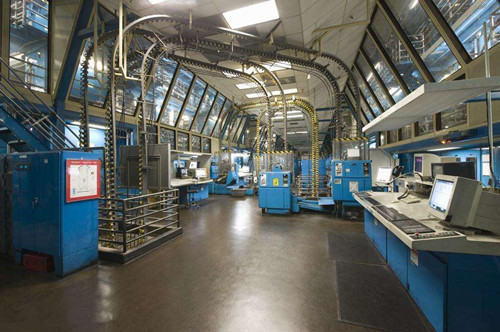
其实,标准化作业管理由来己久,并且在19世纪中后期至20世纪初得到迅速发展。这一时期,资本主义经济迅猛发展,然而,管理水平还很低下,仍处于经验管理阶段,工人劳动效率低、浪费严重,寻找一种合理有效的生产管理方式,成为亟待解决的课题。
大野耐一认为“标准化工作程序说明表及其中包含的信息是丰田生产方式中的重要组成部分。一位生产线工作者要写出一份让其他人能够明白的标准化工作程序说明表,他必须相信这份说明表的必要性……避免瑕疵产品、操作失误、意外状况等重复发生,并纳入工作者的想法,这样才能维持高生产效率”。在这种情况下,诞生了泰勒的科学管理理论。
泰勒所走的方向是“调查影响工作的主要因素,以发现有关因素和时间之间关系的规律”。泰勒认为:“一切管理问题都应该而且可以用科学的方法加以研究,并从中优选出最好办法,若能对其中以体系化、科学化,这种最佳办法便可付诸实现。”
于是,在那一时期西方国家的工厂里,无论是制定劳动定额、工时定额、作业计划还是成本核算,最后都要形成标准。因此,工作标准化在极短的时间成长、发展起来。
第二次世界大战以后,日本积极引进泰勒制,通过制定包括工作标准在内的一系列标准,使企业管理取得显著的效果。为日本工业的迅速复苏做出了卓著贡献。
可是,丰田没有照搬泰勒的科学管理方法,而是在此基础之上,创造性地形成了自己的管理模式。丰田认为,企业要想在所属的行业内保持领先的地位,要有强于对手的竞争力,就必须制定出确实可行的、能授权员工的标准,只有这样,才能持续改进重复性流程。而要充分授权员工,就必须首先把员工当作问题的解决者,而不是只知道接受命令的工具。
这样一来,丰田把传统企业管理中,官僚式由上而下的企业制度取消了,而采取了网络化、有弹性与创新的制度,这就是丰田的标准化作业。
在丰田公司,标准化并不是泰勒时代的“明确写出操作员必须遵循的工作步骤”。具体来说,丰田公司标准化作业具有以下3个特点:
1.由现场监督人员决定具体的标准作业
在以往公司,标准作业一般由IE人员来决定。而在丰田汽车公司,标准作业的各项组成要素,主要是由现场监督人员具体决定的。比如:组长、班长有权决定各台设备生产一个单位产品需要的作业时间和各个作业人员应该完成的各种作业的顺序。在制定标准作业后,组长和班长必须亲自对这个标准完全掌握、了解,并且现场操作,以使作业人员可以对此标准作业完全理解、服从。
丰田认为,只有对现场作业及操作人员非常了解的人才适合作为标准作业的制定者,而班长、组长最符合这个要求。也只有这种标准作业才具有可行性、公平性,也激发了员工的主人翁意识。
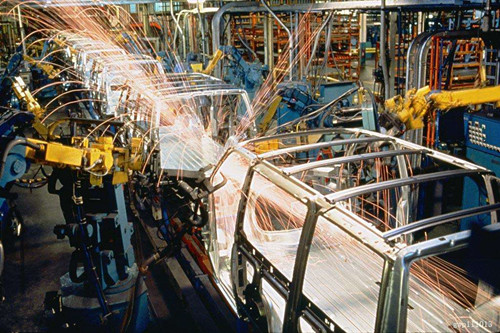
2.标准化作业分为五个特定程序
(l) 确定循环时间。
(2) 确定一个单位产品的完成时间。
(3) 确定标准作业顺序。
(4) 确定在制品的标准持有量。
(5) 编制标准作业书。
3.用循环时间对作业人员进行再分配
对作业人员进行再分配指的是,按生产一个单位产品所必需的不同作业数目和作业人员人数,对人员和材料进行重新分配,以减少作业流程中人员使用量。
由此看来,丰田公司的标准化并不是那种强加于员工的工作标准化,而是把标准化当作一种授权,以提高工作效率、激励员工不断创新。丰田标准化为企业创立了共同合作的团队,解决了劳资关系,因而把以前被视为不利或无效的标准化,变成了有利、有效益的项目。
丰田认为,要实现持续改进,必须先把流程标准化。如果,作业流程杂乱无章法,经常改变,任何针对此流程所做的改进都是无用的。因此,丰田公司的标准化不仅仅是使作业人员的工作可重复且有效率。丰田的标准化己经应用到白领阶层的工作流程中,在丰田公司任何一个角落我们都可以看到标准化的影子。
当丰田公司要开发新的产品,组织新的生产线时,是怎样制定新的标准化的呢?比如,一个企业在一个陌生领域,要投入资金,新产品开发时,怎么把不可避免的混乱情形标准化呢?丰田公司的做法是以均衡的方式把工作标准化。当一项新产品处于早期计划阶段时,他们先把代表工厂所有部门领域的人员全部聚集在一个开放式办公室,形成一支大团队,称为“先导团队”。“先导团队”不仅协助生产,还和工程部门携手合作,发展最初的标准化工作,以在此产品刚推出时使用这些标准化工作,然后再把它交给生产团队,寻求进一步改进。
在丰田公司,标准化作业的目的,是通过必要的、最小数量的作业人员进行有效生产。丰田公司的标准化,首先保证了产品的高质量。在丰田公司,当制件被发现有瑕疵时,作业人员被问的第一句话是:“有没有按照标准化工作执行?”接着,在解决问题时,监督管理者会看着操作人员按照标准化工作说明表中规定的步骤重新执行一遍。如果发现不是操作人员的问题,他的操作完全遵循了标准化作业表,那就表示这些标准步骤必须加以修正:如果发现,是由于操作人员的执行错误,而导致瑕疵产品,此作业人员便会受到相应的惩罚。
实际上,丰田后一种情况发生的概率非常小。去过丰田公司的人都知道,那里的标准作业程序说明表并不是张贴在工作场所内。所有的作业人员都受过执行标准化工作的训练,每个人都必须做到不看表一样能准确无误地执行标准化作业。
其次,标准化作业提高了生产率。因为,标准化让许多无效劳动不再出现在生产作业中,既提高了工作效率,又激发了员工的工作积极性。标准化使均衡化生产成为可能,因为,在实现标准化的过程中,“循环时间”或者说均衡化理念就己经很好地贯彻到作业中了。标准化作业也有助于减少库存浪费。标准化作业中,制品的“标准持有量”在消除多余的在制品库存力面有潜在的力量。
文章来自网络,版权归作者所有,如有侵权请联系删除