首先声明,这个不是讨论法规规定每周上班几小时的工时!
我记得开始工作(IE工程师)的第一份任务就是在产线做作业工时量测,现在回忆起来还历历在目。当时很努力的想要在新任务上展现自己所学,一方面是自己在大三的专题是做工时相关的题目,同时也觉得这个是个很简单的任务,应当可以给老板一些好印象!经过了3个月的奋战,才发现自己小看了这个任务的难度与重要程度。
3个月?真的不夸张,我花了3个月的时间,最后只是把标准和实际有什么差别搞清楚了,但是一点都不遗憾,因为这3个月的基本马步,给了我未来二十多年的制造管理工作中对于工时有了基础的认知。所以今天就来聊一聊标准工时与实际工时之间一些容易混淆的观念。
不准怎么可以成为标准?
常常听到有人说:单位的IE不知道在干什么?标准工时一点都不准!这个是最常被挑战的问题了!所以先很快的科普一下,什么叫做标准工时?
现代对标准工时最一般定义是:「标准工时乃指对于必要之能力受过充分训练的作业人员,在适当的速度和作业环境下执行作业所需要的时间。」
所谓标准时间,乃是在下列条件下,完成一单位作业所需的时间:
1. 采用标准作业方法与设备
2. 在标准化的作业条件下
3. 作业者均具备制程所要求的熟练度与适应度
4. 在不妨害生理健康的情况下
5. 以企业所认定的正常作业速度,完成一个单位作业量所需的时间
在定义里面完全没有提到标准就是要“准”,能够做到一秒不差就叫做好!在标准的设定中本来就有所谓必要的宽放(如生理与疲劳),关键是合理认定的“适当”。所以第一件该说清楚的就是设定标准的目的本来就不是要求“准”,但是要求合理,既然目标是合理,就应该是可以有机会达成(作业人员在上述定义的条件下可以做到)。但事实往往不尽如人意,任何一个因子都可能使得实际作业无法达到(当然也可能超出)。而这也就造成了当实际与标准有了差异时,不明白其原理的人会认为标准一点都不准。有一些没认清管理目的的工程师,受到这个“不准”的压力,就开始以误用实际工时的某种平均方式来形成标准,甚至为了要准,还加上很大的宽放值,来达到准的目的。抛弃了原来在标准工时的设定下应该有的“合理”。
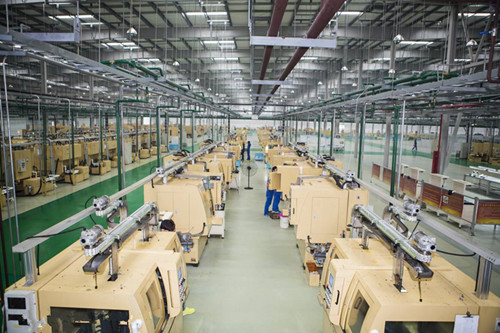
一个持续改善的过程
与其说是标准,其实更像是阶段性的管理目标。
1. 标准工时的起点:
大家想想你所在的企业,当一个产品生成第一版的标准工时是在什么时候?较规范企业应该是在开发的PVT(量产能力确认)阶段,或是新产品导入(NPI)的阶段,当时可能很多的生产作业还在变化就开始设立标准,即使变化还是很多,也一定会先依过去经验先预估一版或是以实际的生产数据以统计的方式来产生一版,这两个方式并没有错误,因为在新产品导入阶段,关注的重点是:如何让产线可以快速的进入量产!
标准工时会随着作业内容不断的调整与修正,目的也是希望协助产线能逐步稳定形成合理的作业规范。产品导入量产前,标准工时是随着制程作业的调整一直改变的,企业管理能力较佳的的体现就是:新产品导入的时间很短(标准工时也会随之稳定下来)。
2. 标准工时的持续精进:
接下来就是进入量产阶段,此时的管理关注是:如何确保交货能够有效的达成,也开始进入效率与成本的检讨。
既然新产品导入量产了,合理的标准已经建立,工时管理的重点:不是消灭差异而是管理差异。为何实际作业有差异的发生?这些差异如何被有效的分析(管理),此时各种改善手法与工具才上场。
找到造成差异的原因(例如:作业手法,治工具,设备参数或稳定等等),这才启动现场的持续改善活动,确定是标准真的不合理、还是人员训练不足、设备稳定度不好还是治工具设计不良或是耗损…。
当差异因子被充分掌握了,才知道标准是否有必要变动。(如果标准作业与规范没有变化,工时为何会变呢?)再提醒说明下:不是消灭差异而是管理差异。
永远要记得总结
当历经新产品导入的快速调整,以及后续不断检讨分析差异,进行了许多的改善,个别产品完成量产的使命了,很多企业在工时管理的过程,忽略了最后一个环节,那就是历程的检讨!
因为企业的许多产品都有系列关系,或是基于类似的制程工艺生产,所以经过这样的改善经验后,下一个接续产品的开发,不就有了一个相当好的对标基础?而且是全周期的参考,除了在个别作业的工时,还可以作为产品爬坡提量的参考,也就是应该会对后续产品提供最佳实证的历程参考。但是目前大部份的企业都忽略了将工时的过程作完整的纪录(改善履历),而这个履历正是提供新产品设计的可量产性(Design for Manufacture, Design for Cost…)重要的指导。
标准工时的管理是伴随产品生命周期的管理,同时产品的BOM以及损耗也有类似的特性,所以同样也可以应用在标准成本的管理上,目前也已经有成熟的信息系统可以协助企业进行工时的管理与后续的应用。所以,千万不要忽略了这看似基础而且又繁杂的工作,对于制造管理来说,是至关重要的一个能力。
文章来自网络,版权归作者所有,如有侵权请联系删除