IE(Industrial Engineering)这个名词经常翻译成工业工程或工业工程管理,但是我从年轻时就认为这指的是生产技术,因为这是从支援技术层面的方式去思考如何提升制造现场的水准。
IE在欧美及日本的产业界当中,对于生产性的提升做出了很大的贡献。随着时代的演进,IE这个名词逐渐消失在制造现场,取而代之的是各式各样的方式不断地出现或消失。
在台湾同时吸收了过去与最新的IE手法,因此我能感受到今后将是跨越实践基础IE的时代。IE是支撑制造业整体的基石,因此我希望回到IE的本质,重新去思考改善、改革与革新的方式。
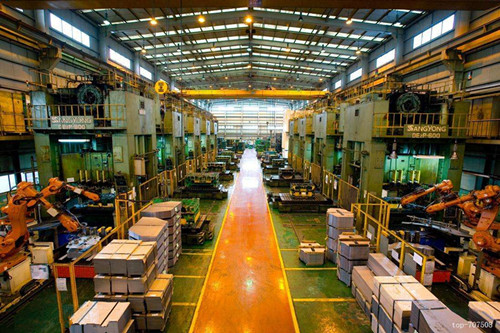
IE的历史
IE在1900年初头,由美国的泰勒(F.W.Taylor)为首,开始进行了“科学管理法”。泰勒的科学管理法当中,最具代表性的实验就是钢铁公司所进行的铲铁砂实验。以每铲一次的量与一天的总量,进行相关研究,并决定出一天的标准作业量。
泰勒为了保持良好的作业效率,并向上提升水准,在设定标准时间时,在教育训练、制作作业计划、铁铲与作业场所的配置等方面,提出了许多方案。
与泰勒同时代的吉尔布雷斯从事建筑业,他利用堆砖头的作业,在消除浪费的动作上进行了实验。堆砖块的作业当中,包含了拿砖块、堆起来、涂水泥三个步骤,并研究了其中的各项动作。确立了标准性的作业之后,决定标准时间的想法为基准,设定出最小动作单位(Therblig)的16个标准动作记号,并决定出动作分析的方式。
当时的IE是以制造现场为对象进行改善与技术提升,泰勒与吉尔布雷斯都曾待过制造现场。此后,IE采用了科学与工学等多方面的要素,开始发展出多面相的经营管理技术。
第二次世界大战之后,当QC传到日本时,IE也开始为人所熟知,广泛地运用在制造业为主的各个企业公司。在提升改善效果的同时,也扩展到更多不同的领域当中。
日本能率协会在1959年出版了“IE”月刊杂志,介绍国内外IE的最新动向以及各种不同的技术手法,成为许多企业的启蒙老师。1982年“IE”与“Manegement”两本杂志合并为“JMA Journal”月刊杂志,虽然“IE”杂志不再单独发行,但是我认为它在23年当中对于IE的发展功不可没。我在年轻时每个月都会阅读这本杂志,从中获得了很深的启发,同时参考书中许多的内容,实践在生产技术与生产管理的业务上。
IE的主要手法
IE的定义如下,“将人、资材、设备(3M)与方法(4M)、资讯或能源所统整出的生产系统进行设计、改善与实施。为了从生产系统所获得的结果进行规定、预测与查核,使用了工程性的分析与科学性的专业知识与经验。”
工程性与科学性是以数值(标准时间)为基准进行系统性的管理,用IE的手法进行时间研究与动作研究,设定出标准作业与标准时间。标准作业或标准时间是工厂的生产技术或生产计划与管理的基础,也是IE所不可或缺的一部分。
主要的IE手法有工序分析、运作分析、时间研究、动作研究、搬运分析、事务分析,我将以个人的见解向各位介绍概要上述六种方式。
工序分析是使用记号将工序的流程图表化,提升流程改善的水准。然而我们时常会发现,一旦制作出图表后,改善活动就停滞下来了。另外,以此为基础有时只有做出了QC工序表,因此整体工序表的制作与数据化是必要的。从整体工序表的观察当中,就能明确地找出其中的问题。
运作分析是指人员与机械的运作状况,进行多次的瞬间观测,并统计出现象产生的发生率。一般是使用瞬间观察法,近来则是使用无人照相机或是摄影机摄影,进行连续观测法,就能够更容易地掌握现场状况。以此配合其他的IE方式,就能够找出改善的方向。
时间研究是将研究对象的作业流程细分化,将各单位加以分解,并使用计时器测量作业时间。从测量结果明确找出改善关键的手法,在设定标准时间上是有效的方式。同时进行开始与完成连续作业的测量因为很不容易,可以先记录各作业的开始或完成时间,进行观测之后,再计算各别时间。测量连续经过的时间时,即使途中的记录发生失误,也能继续进行测量。
动作研究是将作业的内容用动作记号表示,进行动作程度的分析与改善。在多种少量生产当中,运用时间研究的单位作业与细分化作业程度的分析很足够,但是在动作经济的四个原则之下,包含“1.减少动作数量、2.同时活用身体各部位、3.减少动作距离、4.让动作变得更轻松”,因此有意识地进行改善有其必要之处。
搬运分析是在工序分析中,补充搬运工序的部分,和工序分析共同分析搬运、处理、停滞的状态,并进行改善。从物品四处放置开始,直到装箱、排放、搬运车上进行改善。在制造大厂M社的组装工厂中,就是将所有的东西放置在台车上,以拖拉的方式进行搬运。
事务分析是对于事务的业务改善所应用的IE手法,在产业能率大学方式(产能式)与日本能率协会方式(日能式)有类似的应用作法。制作出帐册或资讯的流程图表,找出改善点。最近导入ERP系统的企业似乎开始增加,在导入时制作出业务流程、事务分析与同样的业务改善(BPR),在事务业务的改善上面,能够提升很大的效果。
以上介绍了主要的IE手法。我认为上面并没有特别难的部分,而是以进行制造业的改善为基础,我们在现场所试着做的价值非常大。IE应该是以企业全体作为对象,在各程度上进行多面向的改善活动。
运用在TPS上的活动与事例
许多的企业在导入TPS与QC时,会制作标准作业流程表与QC流程表,ISO9000与14000也是以作业流程表的制作为前提。虽然有许多企业制作流程表或工序表,但是设定标准时间的企业公司似乎不多。
IE的基本是标准作业与标准时间,根据标准时间的设定,实行各种不同IE手法的话,就能获得改善效果。其效果是以降低标准时间的方式,以数据进行查核工作。标准时间的设定并非难事,透过运作分析、时间研究、动作研究的组成,就能够设定出正确的标准时间。简单地进行时间研究、收集实际时间,并以此作为标准时间的开始,就能逐渐提升时间的精确度。
现今我所支援的企业公司在制作标准流程表(SOP)的同时,根据时间研究收集实际时间的数据,并从这个测量值设定出标准时间。以在过去使用过的每个工序或标准工数、前置期去比较的话,标准时间的数值会变得非常小,现场人员本身也感到非常惊讶。
在各个作业的标准时间当中,由于不包含实际上发生各种等待或不良品的修正等浪费的时间,就会成为接近理想时间的数值。
透过标准时间与实际状况比较之后,就能让许多问题可视化,以进行具体性的改善工作。标准时间不只是IE的改善活动,而是从生产计划到成本管理,执行全公司业务的重要基准。
具有悠久历史的IE,是进行TPS与ERP时重要的基石,请大家务必试着去使用IE,必定能从中获得更大的效果。接下来透过活用QC与TPM的小集团活动的方式,以提升公司整体的改善能力。请大家务必试着挑战看看IE各种不同的手法与方式。
文章来自网络,版权归作者所有,如有侵权请联系删除