精益生产管理理念旨在通过消除浪费、优化流程来提升效率与效益。然而,实践中精益生产管理执行不到位的情况时有发生,严重影响企业发展。若要扭转这一局面,需深入剖析问题根源,并采取针对性措施。
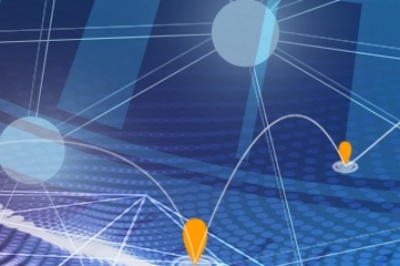
一、精益管理执行困境扫描
流程优化不足是常见难题。部分企业在推行精益生产管理时,对自身生产流程缺乏透彻了解,未能依据精益原则深入优化,致使生产效率提升受限。例如,一些企业生产环节的衔接不够紧密,物料搬运路径复杂,造成大量时间与资源浪费,却未察觉流程设计存在的缺陷。
员工培训缺失也不容忽视。精益管理要求员工具备相应技能与知识,理解精益理念并能在工作中应用。但不少企业实施精益管理时,忽视员工培训环节,员工对精益管理一知半解,难以将其有效融入日常操作,无法发挥应有的作用。
绩效评估机制不完善同样阻碍精益管理推进。由于缺乏有效评估手段,企业难以准确判断精益管理实施效果,无法及时发现问题并加以改进,使得管理改进工作缺乏方向与动力。
二、破局之策:多管齐下扭转乾坤
深入优化流程是关键。企业应运用价值流图分析等工具,全面梳理生产流程,清晰呈现物流与信息流,精 准识别浪费环节。如某制造企业通过价值流图发现产品在车间之间运输距离过长,随即重新规划车间布局,将相关工序集中,大幅缩短运输距离与时间,降低运输浪费。同时,持续关注流程运行情况,定期评估与优化,确保流程始终处于高效状态。
强化员工培训不可或缺。制定系统培训计划,涵盖精益生产管理理念、流程优化方法、操作技能等内容。通过内部培训、外部专家授课、实践演练等多种方式,提升员工对精益管理的认知与应用能力。某企业开展精益管理专项培训后,员工主动参与流程改进,提出诸多有效建议,显著提升生产效率。
构建科学绩效评估机制极为重要。设立与精益管理目标相符的评估指标,如生产效率提升幅度、浪费减少比例、产品质量改进情况等。定期对各部门、各岗位进行评估,并将评估结果与员工绩效挂钩。以此激励员工积极投身精益管理,推动企业持续改进。
供应链管理也需协同优化。加强与供应商沟通协作,确保原材料稳定供应且质量合格。同时,优化企业内部生产计划与物流配送,减少库存积压与缺货风险。通过上下游协同,提升整个供应链的效率与效益。
精益管理执行不到位并非无解难题。企业只要正视问题,从流程优化、员工培训、绩效评估、供应链协同等方面发力,持之以恒推进改进,定能突破困境,实现精益生产管理的良好成效,提升企业竞争力。