搞精益生产,一定会用到建议系统。但是从管理实践上来说,运用成功的并不多。大概归纳一下,主要是以下几个原因。
1、忽视中国人和日本人思维方式的不同,硬搬日本人那一套。
2、负责的人没经验,不知如何下手,挂几个建议箱,收集各种意见而已。
3、咨询工程师,没有实际运营经验,凭想象做事。
举个例子,我见过一个工厂,顾问公司的工程师说要收集员工建议,于是他们就挂了好多建议箱,规定员工每周必须提交两个改善建议。第一次收来了几百条建议。整理以后,里面20多条说厕所里要养盆花;30多条说食堂每天要供应鱼头;还有说工厂门口的树不好看要砍掉,等等等等。。。这些建议不应对,则以后没人再提建议,全部应对要占用大量的管理资源,本来很好的一个事情,变成了打自己的脸。
这个工厂的老板和他聘请的顾问,根本就没搞清楚建议系统怎么运行的,就望文生义,以为挂个建议箱,制定处理建议的程序,建议系统就能好好运行了。实际上这样的建议系统还不如没有。
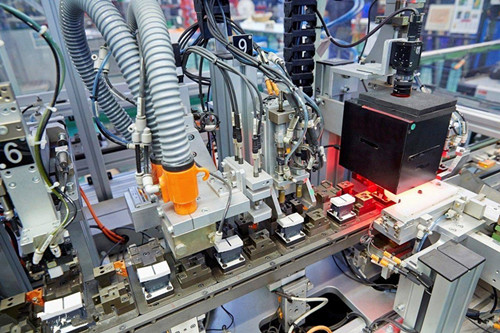
下面再说说,我所知道的运行良好的建议系统。
首先,建议系统建立前,员工和管理者必须是经过TPS知识培训的,只是在不同岗位,培训的范围不同。第二,建议是指定范围的。第三,前期是要有老师充分引导,第四、有些建议的方法是指定的。
建议的范围,不要望文生义,不单是指在什么事情上的建议,而且改善的方法也有限制,否则改善很可能会倒退。在初期,提什么样的建议,都是管理者指定的,养成习惯以后,再放开提建议。
初期管理者指令性的要求提出建议,范围一般如下:
1、跟部门KPI相关的。如下一季度,部门生产力指数上升20%,DCT时间降低20%,库存周转率增加一倍。我要改善什么?这时,部门把任务分解给下面的小部门,为了完成KPI,下面每个小部门必须提出几个建议。这些建议里面,使用方法是指定的,必须是丰田的改善十二种工具。
2、跟CT有关的。我们改善,一般会尽量缩短CT,拉长TT。这种建议就会分解给各班组。其他生产支援的部门,如管设备的部门,建议就是换模时间缩短,更好的保养方法等等,也归到这一类。
3、跟安全有关的。
4、其他改善无关的,都交给行政部门处理。
这里很容易看出,没有前期培训,初期指导,必然会走偏。我现在所见过的顾问公司的人,一般都是工程师出身,没有实际运营经验,在这种事情上没有指导的能力。所以,大部分建议系统,最后都不了了之。
文章来自网络,版权归作者所有,如有侵权请联系删除