精益生产在国内造船业的应用研究
引言:
中国造船虽然有了很大的发展,但是在造船管理和技术方面,我国与日本和韩国相比,还有很大差距,造船效率和造船效益依然低下。世界金融危机的到来,使“船舶市场迅速下滑”,如何化解接单难、交船难,给企业经营管理提出了更高的要求。
造船企业的竞争能力取决于生产成本,造船市场在向有一定经济技术基础、生产成本更低的国家转移,这是造船产业发展的规律。造船企业要想在激烈的市场竞争中成功,就必须把品牌、质量、成本、服务、效率等提高到首要地位,而精益生产管理体系的目标就是高质量、低成本、高效率,可以满足造船企业应对市场变化提升竞争力的需要。实践并推广精益管理的先进造船管理思想,推进现代化造船模式的建立,转变造船模式,大力推行按区域组织生产,以中间产品为导向,壳舾涂一体化,设计、生产、管理一体化,均衡、连续总装造船,不断地改进和完善造船生产过程,减少造船生产中的一切浪费,从而达到缩短造船周期、降低造船成本、提高造船质量的目的。在“十二五”即将到来之际,面临科技、经济、政治、文化飞速发展的今天,把现代造船模式发扬光大是船舶工业重要任务之一,并且精益生产已是迫在眉睫、不容回避的问题。
精益造船的内涵
精益生产模式来自对日本汽车工业的总结,丰田汽车公司是其典型代表,核心思想就是消除生产中的浪费和一切非增值环节,使企业同时具备大批量生产经济性和多品种生产灵活性的能力。1990年美国麻省理工大学James P.W.等人将其概括为精益生产,1996年再将这一系列的方法和理论进一步阐述总结为精益思想:识别价值流、流动、拉动和过程尽善尽美。
精益造船顾名思义就是追求精益求精,是企业保持持续改进、持续发展、持续提升的精神渊源。精益造船由精益生产概念引申而来,是精益生产理论在船舶工业中的应用,首先由美国造船界提出,指从造船合同签约开始到船舶完工交付使用的建造全过程中,通过对全体员工的激励和动员,不断改进和完善造船过程,减少船舶建造中的一切浪费,达到缩短造船周期、降低造船成本、提高造船质量,从而获得更好产品利润的目的。“精益造船”就是以精益生产模式造船。
造船业实施精益生产的主要内容
精益造船内容主要包括:价值流管理、单件流水作业、拉动计划体系、适时生产和无缺陷施工、均衡生产和生产节拍、5S管理、精益质量管理、精益企业文化的建设等。
价值流管理
价值流是使一个特定产品通过任何一项商务活动的三项关键性管理任务时所必须的一组特定活动。这三项任务是:从概念设想,通过详细设计,到投产的全过程中解决问题的任务;从接订单到制定详细进度,再到送货的全过程中的信息管理任务;从原材料到制成最终产品,送到用户手中的全过程中的物质转化任务。价值流图就是指从原料到成品的全部活动(增值与非增值两种)的表达(如图1),其过程既包括信息流亦包括物流,是实施精益生产的关键。作为企业对全部流程(信息流、物流)实现可视化的一种有效工具,通过识别价值流中各种类型的浪费,并对他们采取相应的措施,能够从全局角度改善流程。
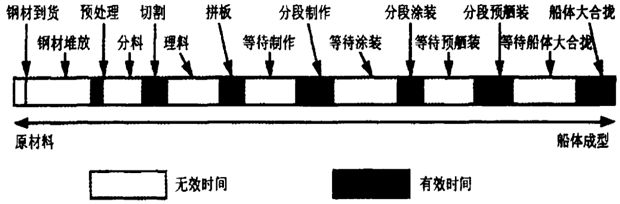
在传统造船模式当中,非增值活动时间远大于增值活动时间。传统的造船模式往往注重提高作业加工的生产效率,精益造船模式更注重于缩短无效时间,减少中间环节的浪费,从而大大缩短生产周期。
单件流水作业
丰田汽车公司认为最大的浪费就是生产过剩。在传统的规模生产模式中,为了扩大生产,追求设备利用率,组织批量生产,生产准备时间长和在制品库存多是组织批量生产的特征,因此生产过剩也就成为必然。理想的精益生产是让每一部件和中间产品都能做到连续不断地生产,按客户(内部和外部)的要求按时完成生产,不提前,也不拖后。把相同类型的中间产品一件一件地连续不断地组织传送带式的生产流程,称为单件流水作业。组织单件流水作业,做到连续不断生产,实行零库存管理,就可以减少生产过剩。只要单件流水作业一出问题,就需要立即解决,否则生产就会停顿,直接影响后续生产。实现单件流水作业后,质量问题能够迅速反馈,要求作业者马上解决,否则就会影响下道工序生产。作业者通过现场施工,学会思考,提高发现和解决问题的能力,许多好的预防措施、生产组织形式、工作标准也就应运而生,生产效率随之大大提高。
拉动计划体系
传统造船模式通常由管理部门制定公司生产计划,然后层层下达计划,由下面制定具体的实施计划。这样的计划要求纵向到底、横向到边,从上到下、从前向后地推动,是推动计划体系。同时要求计划策划人员必须熟悉全公司的情况和资源,否则计划就难以落实。一般情况下,计划工作很难做得非常具体、细致,这样,计划执行的随意性比较大,执行过程的控制难度较大。
单件流水作业需要按照客户需求建立从后向前、由下而上的拉动计划体系。由后道工序向前道工序提出订货计划,前道工序则严格按照后道工序的交货要求,不提前,也不拖后地安排生产。在单件流水作业生产社,每…道工序既是生产者,又是客户;既需要满足下一道工序的交货要求,同时又需要向上一道工序提出订货要求。用于这种上下连接生产的管理方法,在日本叫做看板管理。
精益造船的单船生产计划是从后向前,按照客户拉动的原理,由每一道工序的作业组织按照流程所需的时间平衡,组织有节奏的均衡生产。
适时生产和无缺陷施工
适时生产和无缺陷施工是精益造船模式的两个重要理念,是造船质量、成本和周期目标实现的根本保障。
适时生产是在需要的时候,按照需要的数量,生产需要的产品。适时造船就是要组织单件流水作业生产线,运用成组技术原理,按照造船作业的阶段、类型和区域,组织柔性的相似的中间产品分道或流水的作业生产线,真正形成一件接着一件、按照生产节拍交付产品的传送带式生产。组织适时生产的最大好处就是可以大大减少人工和物资的浪费,没有库存,没有闲置劳动力。
无缺陷施工就是要把所有的可能出现的施工质量问题都消除在源头,这就需要组织质量的自主管理,贯彻“质量是做出来的”的思想,谁做谁检查,谁做谁负责修复缺陷。取消专检,以自检和互检为主。要求作业者严格按作业标准一次作业合格,决不允许次品流入下道工序。无缺陷施工的最大优点是把质量问题消除在源头,可节约大量人工检验和缺陷返修成本,缩短了船舶建造周期。
均衡生产和生产节拍
为了保证生产能够象流水线一样连续不断,同时又要满足市场和客户(内部和外部)的产品需求节奏,需要组织均衡生产,让生产处于一种有节奏的状态当中。这样,就需要按照生产节奏的要求,运用成组技术原理,按照作业的阶段、类型和区域,合理设计单件流水生产的作业量,计算出生产节拍。生产节拍也可以称为客户需求周期,生产节拍=总生产时间/客户需求数量。对于造船,生产节拍可以是每个小时交付一个托盘的管子,或者每天合拢三个标准分段。生产节拍是生产管理的一个目标,通过建立生产节拍组织均衡生产,让生产更加流畅。
生产节拍不一定等于实际生产周期。比如,管子车间每个小时可生产交付一个托盘的管子,而下道工序只需每1.5小时交付一个托盘的管子。这样,生产周期就小于生产节拍。如果只需满足生产节拍要求,生产能力就会放空,势必造成人员等工或设备能力闲置现象;如果上一道工序连续不断地生产,就会造成库存积压。这两种情况都将造成浪费。反之,如果生产周期大于生产节拍,为满足生产节拍的需要,就需要加班或提前安排生产,储备一定库存,这样,无论加班或加大库存,都需要增加成本。因此,在组织均衡生产的过程中,一定要追求生产周期与生产节拍基本保持一致。按照精益生产理论,造船分段制造完全可以组织节拍生产,如图2所示。
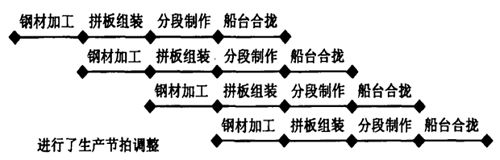
5S管理
一个好的工作场所,应该清洁、整齐、稳定有序的,且有一系列可视的工作标准,保证所有工作都处于有标准的可控状态。只要整个系统出现一点偏离工作标准的现象,这种偏离就会在该系统中迅速暴露无疑。同时,要求系统具备迅速排除这种不正常,恢复稳定的工作秩序的能力。
精益造船模式将实现上述要求的管理称作5S管理,即整理、整顿、清扫、清洁、素养。5S创造了一个持续改进的PDCA循环过程,提供了一个可视化管理的环境。5S可定义为五个工作阶段:(1)定义产品价值链(明确有价值的生产环节);(2)取消无效工作环节(制定改进措施);(3)制定新的价值流(重组价值链);(4)由客户拉动价值链(组织适时生产):(5)保证持续不断地改进(PDCA循环)。实施了5S管理以后,所有问题表面化了,问题可以得到充分暴露。这样,就可以立即采取有效措施解决问题。缺损的物品或库存可以及时得到补充;产品质量问题可以得到及时解决;不符合标准的工作状态可以及时得到纠正。5S的可视化管理可以涉及到船厂管理的每一个角落,可以包括钢材的下料号料、计量器具、工装设备、部件和在制品的库存,以及所有在制品的生产进度管理等等。
在船厂不断推进5S管理,可以持续改进作业标准、改善作业环境,给工人创造良好的作业环境,把所有操作设备和工具放在最方便作业的地方,让工人能够全神贯注地作业。
精益质量管理
精益生产方式在质量管理方面的观点就是“质量是制造出来的,而不是检查出来的”。按照精益生产的要求,保证产品质景的职能应转移到操作人员,实行工序质量控制,做到全面质量管理。在造船精度控制、人员素质和防错措施方面均有严格要求。其中造船精度控制是精益造船的重要特征,就是用数理统计的方法,通过对造船生产过程中的加工公差和焊接热变形的精度控制,用补偿量代替余量的办法,减少造船加工、装配和焊接当中的无效劳动。精度管理可以极大地减少造船生产过程浪费,减少无效劳动,降低作业难度,实现高效焊接,提高产品质量。
精益企业文化
“人”是精益造船模式中最具活力的因素。一个船厂要建立精益造船模式,必须要创造一种良好的企业文化,要让全体员工在精益造船模式的运用中去不断地完善自我。因此,精益造船要求全体员工参与生产过程中的各项管理工作,包括生产进度、质量、设备、安全、环境、劳动力安排等每一个生产环节。作业标准和精益生产方式强调发挥人的潜力,要把精益生产的思想灌输到每位员工的心里。每位员工在工作中不仅要执行t级的命令,更重要的是积极参与,起到决策和辅助决策的作用。通过团队工作方式、提案制度、质量控制小组、目标管理等一系列具体方法,调动和鼓励职工进行“创造性思考并注重培养和训练工人以及各级管理人员的各方面技能,最大限度地发挥和利用企业组织中每一个人的潜在能力,提高职工的工作热情和兴趣。
结束语
精益造船是一种先进的造船模式,是船厂建立现代造船模式的必由之路。其精髓是团队合作、信息畅通、节约资源、消灭浪费、持续改进。通过深化管理内涵来缩短造船周期和增加造船产量;通过动员和激励全体员工,从减少浪费的点点滴滴做起,逐步实现精益化的造船生产方式,从而提高船厂的竞争能力。因此,船厂要实现精益造船模式,需要不断地领导和教育全体员工,用精益造船的理论和方法进一步统一思想,结合船厂的造船实践,探索精益造船在船厂的具体实现形式,从现场管理开始,从改善入手,坚持数年,必见成效。使中国的船舶工业在新一轮的产业梯次转移过程中真正成为世界第一的造船大国和强国。
分享:冠卓咨询
说明:转载请注明“精益网”