01
What:什么是SMED?
SMED,Single Minute Exchange of Die,“一分钟即时换模”,通常叫快速换模,也叫快速换产,是一种快速和有效的作业切换方法。
这一概念指出:所有的转变或者启动都能够并且应该少于10分钟——因此才有了单分钟的说法,所以又称单分钟快速换模,用来不断改善设备快速调整这一难点的一种方法,尽可能的将换线时间缩到最短,甚至实现即时换线。
它可以将一种正在进行的生产工序快速切换到下一生产工序。快速换模也常指快速切换,能够促使并且常常是用于启动一个程序并快速使其运行,且处于最小浪费状态。
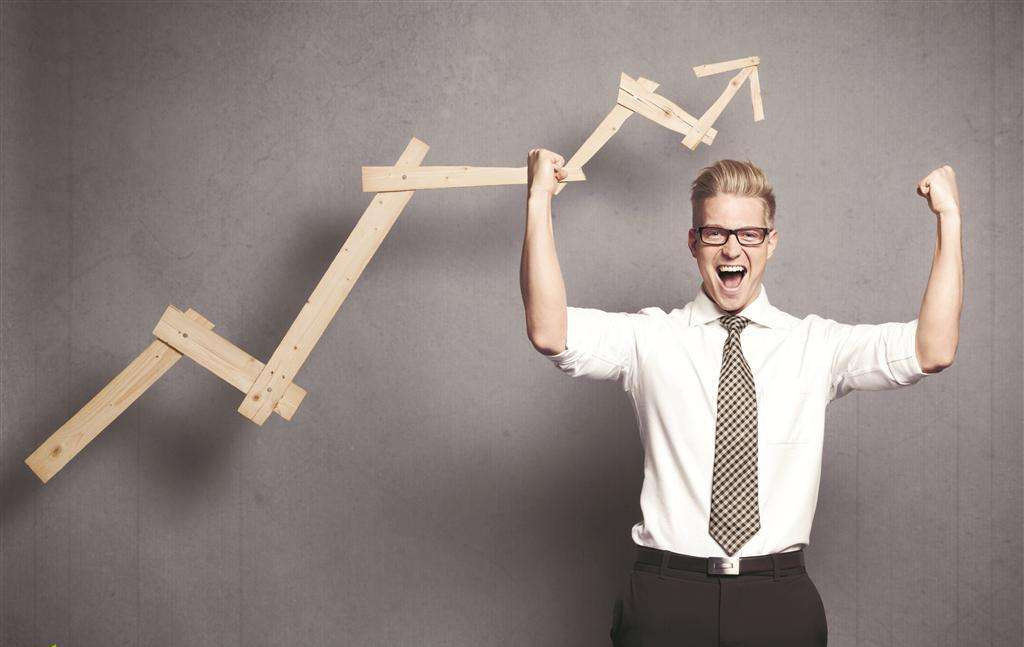
02
Why:SMED的目的?
关于SMED的目的和效益,有多种说法,但本质上并不是为了提高生产效率,当然除改善瓶颈工序之外。
我的观点如下:
1. 主要减少工作操作的时间浪费,增加切换次数,实现多品种换线,从而提升产品柔性和增加不同客户需求。
2. 加快了半成品或成品的流速,从而缩短制造周期,缩短交货时间即资金不压在额外库存上,节省成本。
3. 减少在制品数量,使得不需额外的库存即可满足客户要求,资金成本节省。
4. 减少调整过程中可能的错误,缩短切换的停顿时间意味着柔性和更高的生产效率,也就是提升设备的OEE。
03
When:SMED的起源?
追溯SMED的起源是日本50年代初期,由Shigeo Shingo(新乡重夫,IE工业工程领域著名品质管理专家,丰田生产体系创建人,
曾提出“零损坏”就是品质要求的最高极限并发表以“防呆”即Poka-yoke系统去完全消除错误)在丰田汽车公司摸索发展起来的一套应对多批次少批量、降低库存、提高生产系统快速反应能力的实用技术。
Single一词在这里的意思是小于10分钟,当新乡重夫先生亲眼目睹换型时间居然高达1个小时,他的反应“必须让流动顺畅起来”。
基于他的丰富经验,开发了一个可以分析换模过程的方法,从而为现场人员找到了换型时间为何长的原因以及如何相应减少的方法。

在他领导的多个案例当中,换型时间甚至被降到了十分钟以下,因此这种快速换型方法被冠为“单位分钟快速切换”。
最初使用在汽车制造厂以达到快速模具切换(Exchange of Dies),帮助丰田公司的产品切换时间由4小时缩短为3分钟,后来在众多企业实施论证过。
因此,从广义理解和应用领域讲,可以称之为“快速切换”,不论模具、产品和生产线等不同区域和行业。
04
Example:SMED典型案例
分享SMED的一个典型案例:F1世界一级方程式赛车的轮胎切换,可以让我们非常直观的了解其价值。
自1950年国际汽联第一次举办了世界锦标赛,F1已经走过半个多世纪,我无从得知哪年开始考虑赛车轮胎更换,但有一点确信的是途中换胎时间记录,从80年代的1分钟到现在的十秒之内,其方法和工具都经过了巨大改良,究其原理就是SMED。
F1赛车更换轮胎最快在2秒内
05
How:SMED的实施步骤?
所谓“快速切换”,顾名思义,其目的旨在缩短作业转换的时间,而其关键点又在于划定内部作业转换和外部作业转换,并将内部作业转换尽可能地变为外部作业转换,然后尽可能的缩短内、外部作业转换时间。
在SMED的实施导入过程中,通常分4个、5个或6个步骤完成一次项目改善,关于步骤数量的说法不一,但是都得运用系统的方法,循序渐进的缩短换线时间。
笔者在企业辅导中,通常以下面6个步骤作为基准:
1. 观察当前流程,计算整个周期时间;
2. 区分内部和外部的操作和动作要素;
3. 内外分离,将内部作业转移到外部;
4. 减少内部工作,缩短内部作业时间;
5. 改善外部作业工序,减少操作时间;
6. 操作程序标准化,即最佳实践固化。
另外,快速切换的主要着眼点是减少切换是生产线换线停顿的时间,这个切换停顿的时间越短越好,人工操作时间反而其次,这是80%的要素。
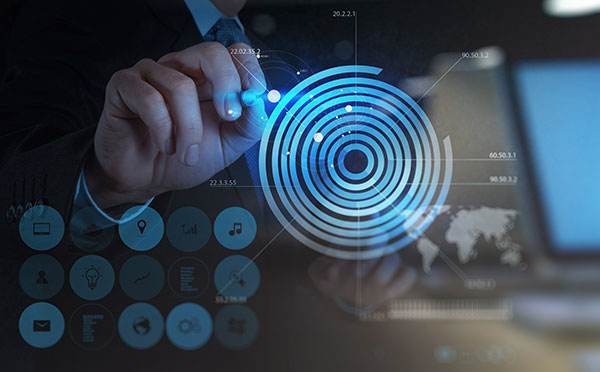
06
根据上述六大步骤,实施SMED可以概括为三个基本要点:
1.“内部变换操作”和“外部变换操作”;
2. 减少“内部变换操作”动作;
3. 缩短“内部变换操作”时间。
当然,如何改善操作的时间,需要辅助其他技术,譬如5S、可视化、IE、标准作业等。
最后,还是用我喜欢的管理大师德鲁克的那句话作为结束语:管理不在于知,而在于行。实践才能了解难易。
文章来自网络,版权归作者所有,如有侵权请联系删除
“感谢冠卓咨询老师对项目组的全程辅导,通过做项目我们学会了如何用系统科学的方法分析研究问题;开阔了我们的视野并让我们的管理人员明白了团队协作的重要性。”
———北京某公司总经理 苏先生