一、六西格玛的起源与发展
近几年来,六西格玛质量管理的风暴正席卷全球。不仅仅涉及企业,还涉及教育和其他领域。20世纪80年代,摩托罗拉创建了六西格玛的概念和管理体系,并全力应用到公司管理的各个方面。摩托罗拉从开始实施六西格玛管理的1986年到1999年,公司平均每年提高生产率12.3%,不良品率只有以前的20%,节约制造费用总计超过110亿美元。由于推行了六西格玛质量管理,使得摩托罗拉获得了马尔科姆・鲍德里奇美国国家质量奖。在摩托罗拉获得成功以后,美国通用电器(GE)、IBM等一些著名跨国大公司也纷纷采用“六西格玛管理法”,并且都取得了可喜的成绩。
二、“六西格玛管理法”与传统质量管理法的对比
六西格玛管理是在传统质量管理的基础上发展起来的,所以,传统的质量管理方法和工具仍然是六西格玛管理的重要工具。
(一)六西格玛强调业绩测量的作用在“六西格玛管理法”中常提到几句谚语:“直到我们测量了我们才能了解”;“我们不测量我们认为没有价值的东西”;“我们不重视我们不测量的东西”。因此,六西格玛强调测量的作用。这是与传统质量管理方法完全不同的。在“测量什么”上,传统的质量管理方法针对产品特性的测量比较明确,但对于业绩的测量却比较含糊。而“六西格玛管理法”强调按顾客的需求和企业的发展重点测量业绩的各个方面,如交货期、顾客满意、成本、库存、服务特性等。
通过对业绩的广泛测量,寻求业绩突破和改进的空间。
(二)“六西格玛管理法”和传统的质量管理方法对于劣质成本(COPQ)的认识不同劣质成本是指由于质量不良而造成的成本损失。劣质成本包括直观部分和隐含部分。就像冰山一样,传统的质量管理方法只能统计露在外面的部分,如报废、返工返修、保修费用等,这些成本损失占销售额的5%-8%。而冰山还有隐藏在海下面的部分,这就是隐含的劣质成本,包括:未按时交付的罚金、库存积压、紧急订货而多付的费用、工程更改不到位引起的报废返工费用等。这些隐含的成本损失要比直观的部分大得多。这部分成本损失占销售额的15%-20%。
已远远超出了利润。而六西格玛管理能将直观的和隐含的劣质成本都考虑在内,将劣质成本控制在销售额的1.5%左右。所以,六西格玛关注的主题不只局限在降低生产过程的缺陷,还要消除工作过程的缺陷,提高工作过程的质量和效益。
(三)完美的质量源于质量设计阶段
质量设计是将产品或服务形成的每一环节进行无缺陷设计。传统的质量管理方法是事后测量或事后控制,也就是说,通过严格的检验来控制和保证出厂或转入下一道工序的产品质量。六西格玛管理强调产品形成的各个阶段中出现的所有问题都将进行通盘考虑和安排,通过预先发现质量问题而获得一种主动权,而不是被动地应付出现的质量问题。摩托罗拉在推广“六西格玛管理法”过程中,其产品质量就是采用了无缺陷设计,以至于产品的检验过程基本取消了。

三、六西格玛质量管理指标
选取六西格玛到底是一种什么方法,能取得如此惊人的业绩,这主要源于六西格玛管理水平的指标在质量管理过程中的有效和科学的利用。衡量六西格玛质量水平的指标有三种:
(一)西格玛水平Z
现代质量管理中要求组织应以满足顾客要求为目标,所以,使用西格玛水平Z作为满足顾客要求程度的业绩测量。在这种测量中,我们通常把每个测量值相对于顾客要求的偏离程度考虑进来。
西格玛Z水平高,意味着满足顾客要求的能力高。西格玛Z水平低,意味着满足顾客要求的能力低,意味着质量、成本、周期的损失。
统计资料表明:对于一个三西格玛水平的企业来说,提高一个西格玛水平可以使利润率增长20%;产出能力提高12%-18%;减少劳动力12%;资本投入减少10%-30%。
(二)DPU、DPO、DPMO
DPU(defectperunit,单位缺陷数),
计算公式为:DPU=缺陷总数/单位总数,表示平均每个单位上有多少缺陷;DPO(defectperopportunity,单位机会缺陷数),计算公式为:DPO=缺陷总数/缺陷机会总数,表示单位缺陷机会上有多少缺陷;DPMO(defectpermillionopportunity,百万单位缺陷机会数)计算,公式为:DPMO=DPO×1000000,表示百万单位缺陷机会缺陷数。
一个正态分布的过程,其超出规范限的缺陷百分比与西格玛水平是一一对应的,根据这个规律,可以通过测量缺陷的比率,估算过程的西格玛水平Z,并以此作为满足顾客要求的能力。
经统计,西格玛水平越高,说明百万缺陷机会缺陷数越低,越能满足顾客需求。
(三)首次产出率(FTY)和滚动产出率
(RTY)很多企业中,只要产品没有报废,在产出率上就不计损失。因此掩盖了由于过程输出没有一次达到要求而造成的返修成本的增加和生产周期的延误。用FTY或RTY测量过程可以揭示,由于不能以此达到顾客要求而造成的报废和返工返修以及由此而产生的质量成本和生产周期的损失。
FTY(firsttimeyield,首次产出率)是指输出过程一次就能满足顾客要求。RTY(rolledthroughputyield,滚动产出率)是构成一个整个过程的子过程的乘积。RTY=FTY×FTY×…×FTY。表明一个大过程是由很多子过程构成的。
传统的质量管理方法是更多地注重交验合格率,如果我们用RTY来测量的话,可以发现越是步骤多,越是技术含量高的过程对FTY的要求就越高。如果每个子过程的FTY都是99%,那么有50个子过程构成的大过程的RTY只有60.5%,也就是说,将有40%的过程须经过返工或报废处理。也许经过返修处理后,过程的输出可以100%交付顾客。用我们传统的产出率统计法,这个过程的输出率是100%。但事实上,这个过程存在着质量、成本和周期的巨大损失,而这些损失是竞争力的损失。
上面三种六西格玛水平的表示方法同时也是六西格玛业绩测量的三种方法,他们基本覆盖了对产品、服务、销售、管理等所有类型的测量。对不同过程、不同顾客和不同要求,我们都可以将顾客或过程要求量化,用不同的测量指标评价我们的业绩与要求之间的差异,以及我们满足要求的能力。但是,不论什么样的指标我们都可以转换成西格玛水平。这样,我们就可以在同一平台上将不同的过程进行对比。
四、六西格玛管理的组织
六西格玛的组织是推进六西格玛管理的基础,而六西格玛管理的一大特点是需要专业的管理队伍来组织实施六西格玛管理。这个专业的管理队伍包括倡导者、黑带主管、黑带、绿带。
其中,倡导者是企业高层管理者中负责六西格玛实施的管理者。负责部署西格玛的实施和全部支援工作。负责确定或选择六西格玛项目。跟踪或监督六西格玛的进展;黑带主管是六西格玛实施技术的总负责。协助倡导者选择项目、制定实施计划和时间框架表,向黑带提供六西格玛高级技术工具的支援,负责动员、协调和沟通;黑带是企业推行六西格玛管理的最关键力量。来自企业的各个部门,经过六西格玛革新过程和工具的全面培训,熟悉六西格玛革新过程,负责指导或领导改进项目。对绿带提供培训和指导;绿带是经过培训,在自己的岗位上参与六西格玛项目的人员。
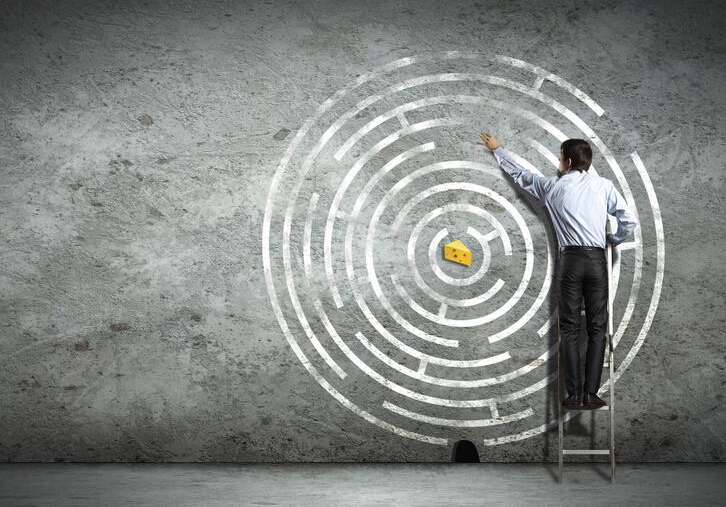
五、结论
企业实行六西格玛管理方法可以缩减企业的劣质成本。这是最直接的利益体现。由于六西格玛管理的介入,可以发现企业内部流程中的低效率点,利用六西格玛的方法和工具,降低成本提高效率,会得到可观的经济效益。统计数字显示,如果一个企业的流程水平达到4左右,企业的劣质成本占到企业销售额的15%-25%。当一个企业的流程水平达到5时,劣质成本就会减少到5%-15%,而6水平的企业劣质成本占到整个销售额的1%。正因为这个原因,每一个六西格玛项目可以带来约80-120万元的财务回报,而组织中的每个黑带每年可以完成4-6个六西格玛项目。
实行六西格玛管理方法,可以帮助企业打造一流的企业文化。六西格玛管理的精髓在于从设计过程中改进和保证产品质量,而不是从结果中检验控制质量。这样不仅减少了控制质量的程序及随之的返工成本,更重要的是培养了企业员工的“做一次就好”(Doitrightfirsttime)的质量意识,并把这种质量意识融入企业文化中,逐渐成为领导的主流文化。六西格玛管理方法提供了一套改善企业流程和企业文化的运作方式和工具,具有很强的操作性。
文章来自网络,版权归作者所有,如有侵权请联系删除
感谢冠卓咨询老师对项目组的全程辅导,通过做项目我们学会了如何用系统科学的方法分析研究问题;开阔了我们的视野并让我们的管理人员明白了团队协作的重要性。
——北京某电器公司