企业既不能盲目地推进自动化、机器换人,又不能停留在大量使用人工的作业方式,需要将自动化设备擅长重复性劳动和高速度的特点与工人的灵活性和判断力有机地结合起来,从而在保证产品质量的基础上,最大限度地提高生产效率。
我们简单看下自动化的发展史,
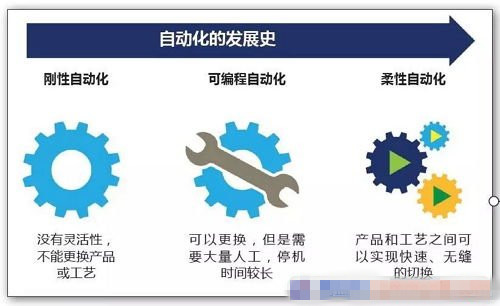
自动化已经从刚性的、只生产一种产品的方式,向柔性、可以无缝切换生产多个产品的方式过渡。
刚性自动化(Fixed Automation)主要设计用于反复高效地生产单个产品。过去,往往只产生一种或有限种类的产品,而且产量很大、变化很小,因此这种模式在生产车间运行良好。由于前期设备成本要低于柔性解决方案,因此对这类生产活动而言,刚性自动化非常适合。如果只生产单一部件,产量就可以得到优化。但是,模块化通常不是原始设计所考虑的部分,这就意味着将机器设备转换成支持多个产品配置时,从经济方面考虑往往并不划算,因此实施比较困难。
随后出现了下一代自动化——可编程自动化(Programmable Automation),旨在实现安装实施后允许某种程度的可配置性。这包括编写新的代码来执行新运营的能力,当然这需要手动操作机械装置来进行转换。缺点是,转换过程往往劳动强度大,需要较长的停机时间以便更换工具和更改编程。
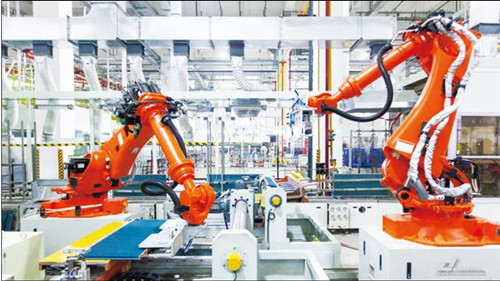
更现代的方法是柔性自动化(Flexible Automation),设备操作人员按下按钮,就可以利用配方控制和机械自动化无缝地将一个进程转换到另一个。这使制造商能够在同一台机器上生产更多的产品,前提是该机器的设计具有生产其它产品的能力。柔性设备采用机电自动化,将快速、可重复的过程转换为位置控制。这允许生产线生产各种各样的产品,而停机时间却很短。
不同生产模式的制造企业,生产自动化程度差异很大:
1)对于采用大批量重复生产模式的企业,例如电子元器件、标准件、制药、食品、饮料、钢铁、化工等行业的制造企业,无疑需要最大限度地实现自动化、少人化,甚至无人化,人的参与是该行业生产过程中最大的污染源。
2)对于采用小批量、多品种生产模式的企业,例如各类按订单生产(MTO)的机械制造、汽车零部件和电气产品制造企业,则应该强调人机结合,将工人的智慧和经验与自动化设备和产线相结合。对于小批量、多品种,以及单件小批生产的企业,推进零部件的标准化、系列化、模块化具有十分重要的意义。模块化程度越高,就越有可能实现生产和组装环节的自动化。
目前很多盲目上自动化的公司都接受过这样的教导:为了提高效率,必须提高机器的利用率。即为了最大限度地利用机器,我们必须做到以下几点:
让设备不间断地、尽可能快地运转,这将会造成过量生产浪费;
保留额外的人员以维持机器运行;
增加在制品存量以掩盖问题,维持机器运转。
换句话说,盲目追求自动化或者机器利用的最大化就是在制造浪费!
相比之下,丰田公司设法最大限度地利用人力 - 人的灵活性带束的好处要大于机器利用率带来的好处。
比如说,操作员可以做到:
只要有需求,就可以从一台机器转到另一台机器进行生产;
可以轻松地为机器装载需要加工的部件并传送部件,而具有自动装载和自动传送功能的机器成本以指数形式增加。
轻松调整工作周期以响应需求的变化。
与大型、复杂的机器相比,小型、简单的机器更可取,因为它们具有以下特点:
更便宜(而且往往能在内部制造出来);
更稳健(很少有移动部件);
可以轻松适应需求的变化(如果需求加倍,我们可以增加一台机器。如果需求减半,我们可以在低成本的情况下让机器闲置一般时间)。
精益系统标准作业的重点是人的运动,追求的是顺畅、安全、以人为中心的工艺流程。TPS倡导在机器设备进来之前,就开始研究布局,把机器也当做人一样分析,研究机器是否符合人的动作。
文章来自网络,版权归作者所有,如有侵权请联系删除