全世界都在学丰田,可同样一件事,有人做得好,有人做得差。为何如此?因为每个企业就像每个人一样,所在维度不一样,思维方式不一样,结果也不一样。看看你的精益在第几维?
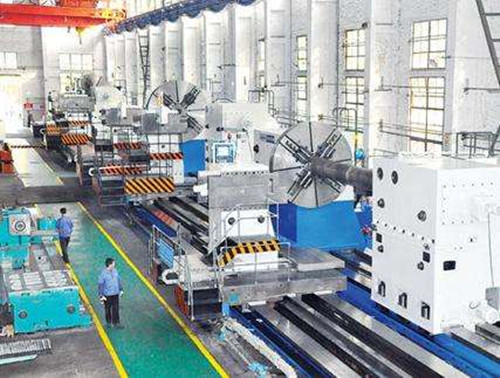
第一维 拿来就用,激歌猛进
看到JIT就学JIT,听说同行在做TQM也立马做TQM,也立马设立改善协调岗位。成立个精益办就想,一两年就想把精益做到高水平。
一定要给自己企业贴上精益的标签。可精益更像一块遮羞布,不知干什么时干精益,不能比别人落后干精益,现场不洁净干精益,开会时精益是炮弹,而且这颗炮弹可以外挂糖衣,也可以鲜血淋漓,是办公室政治的最佳武器!
第二维 照虎画猫,自建体系
自TPS,丰田生产系统被美国人总结提出为精益生产方式之后,全世界范围内的制造企业掀起了学习丰田的热潮,各个建立诞生了自己的系统,GPS,CPS, HPS等等,各自有各自的“丰田屋”和PDCA图。
丰田的体系是很全面的,已经建立了从自上而下的管理、自下而上的支撑体系,企业经营哲学(文化层面)——经营管理会计(财务层面)——生产管理体系(管理层面)——现场稳定执行(工具方法层面),不可能随便截取任何一个层面的理念、工具、方法来直接照搬到企业内,用改善家铃木老师的话说,没有考虑过企业软环境,就像没有搞清楚操作系统就装了APP。
第三维 直面问题 水到渠成
TPS的精髓是发现实际问题、解决实际问题。丰田是从百废待兴的战后日本爬起来的,丰田当时面对的问题是没钱,没钱,还是没钱,可是还是要搞汽车,所以问题就是在没有钱的环境下搞汽车,所以首要问题节省一分钱,不能买那么多钢材,不能雇佣那么多人,不能买自动化生产线,连在制品都不能过多。而如今,你的企业真的有像当时的丰田那样缺钱吗?你今天的核心问题是啥?Q,C,D中C还是你真正的问题吗?很多公司其实只想复制丰田生产方式的表面,却不想直面问题,致力于更困难、必须花更多时间的层面。但如果能锁定最关键的问题解决掉,也许你的所谓的XPS系统也就水到渠成了。
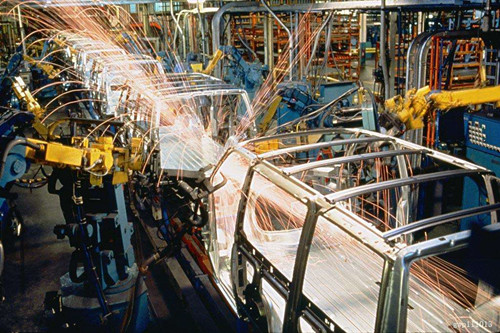
第四维 跳出系统 做对精益
想象你做过的一个噩梦,你在梦中被人追着到处跑,你喊人没人应,不管你怎么努力奔跑,也躲不掉,这是第一序改变。除非你惊醒,才能跳出这个噩梦,醒来是第二序改变。第一序改变是系统内的改变,改变的是状态;第二序改变是系统外的改变,改变了系统的结构,所以才改变了结果。这是斯坦福大学教授保罗•瓦茨拉维克在《改变》一书中提出的概念:第一序改变和第二序改变。
如果说我们谈的前面几个维度的精益都还在生产运营这个序中,而现在讲到的是,难道只能在生产阶段才能改善吗?工程部门不能改机器使得它更符合顺畅、安全、以人为中心的工艺流程吗?其实这个一改,可能后面SOP的问题都不复存在,还哪来的SOP阶段的改善。
另外,是不是整体运营效率的提升就能产生效益呢?精益战略的部署是否正确呢?如果你站在比你高层级的位置看待精益这件事,会是怎样一个PICTURE呢?
层级问题的特征是“低维度思考,低层级努力”。 在这个纷繁复杂的世界,我们一生面对的难题都处于一个又一个复杂的多层系统中。由于低层最容易看到和最好把握,因此我们大多数人往往在这一层努力,而答案不一定在这层。多层系统的特点是上层决定下层,当下层没有答案时,要向上一层寻求原因。
第五维 授权员工 拥抱创新
何一个已知系统若出现一个bug,一定要用一个更大的系统来统一它,才能解释它。bug是悖谬点,更是机会点。我们认为系统之内是常识,跳出系统之外看是见识。见识比常识更重要。牛顿的定律仅适用于低速的宏观的物体,在一个三维的世界里解释的通。但若在微观世界里,若把比如时间这个纬度加上去,就完全不适用了。也正是因为这个BUG,后面才会有相对论,才会有量子力学。
回到企业,身居高位的各位管理者,你的认知系统里难道没有BUG?你们或许会觉得一个由生产工人采取的意想不到的创造性行动让你感到害怕,你觉得他破坏了稳定。但在这个时代,只要搭上技术和互联网的翅膀,就是一个来自现场的优秀改善可能会颠覆甚至重塑整个行业。
所以,我们看到,有人从物流包装中找到机会,改善纸箱包装者的操作,也改善用户开箱的体验,做出一款不用胶带的拉链纸箱,影响了全世界的包装行业。
当丰田最穷的时候,是丰田的全体员工全员改善拯救了丰田,同样,在在VUCA的时代,真正能拯救企业未来的是每一个被赋能的员工!
文章来自网络,版权归作者所有,如有侵权请联系删除