精益生产是企业发展的一种方式,推行精益生产是各企业现阶段应作的工作。但是相对于中国企业来说,推行精益生产还是十分困难的。
“我希望你们打倒我,但是你必须先强过我,你强不过我,对不起,你就必须老老实实跟我学习。”
2002年4月,在中国一汽集团与日本丰田汽车结成战略伙伴的前夕,丰田汽车专门派出公司生产调査部的专家朝仓正司前往正酝酿着未来生产丰田汽车的一汽轿车公司,任务是指导一汽轿车的生产管理,也就是传授世界著名的能够为企业赚钱的丰田生产方式(精益生产)。
朝仓正司在一汽轿车公司的生产现场巡视一周后来到会议室,陪同参观的中国同行例行公事地希望他提些宝贵的意见,这位丰田生产方式专家突然脸一掉道:“我知道你们毎个人心里都想说什么”,转身他在黑板上写了一句话:打倒日本鬼子。脸上没有一丝笑容的朝仓说:“我希望你们打倒我,但是你必须先强过我,你强不过我,对不起,你就必须老老实实跟我学习。”闻听朝仓正司如此狂妄之语,在座的一汽轿车的诸多二级经理一时深感愤怒,有人甚至冒出动手揍他的念头。但是,很快理智战胜感惰,一名当事者事后说:“我们后来一想,他说的话,一点毛病没有。你想打倒他,你手无寸铁,怎么打倒?”算起来,这是一汽历史上第三次幵始学习丰田生产方式。
1990年代,一汽变速箱厂引进日野LF06S型6档同步变速箱,同时也再次引进精益生产,结果在没有增加多少设备、人员和资金的情况下,生产能力由8万辆提高到12万辆。当时的厂长耿昭杰提出“把推行精益生产方式作为一汽继换型改造、产品结构调整之后的第三件大事来抓”。
看起来学习获得了相应的成效,一汽轿车最终利用现有资源高效率地生产出了高质量的马自达6型轿车,它也由此成为一汽学习精益生产的典型。但是内部人士表示:“我们学习丰田生产方式,还只是一个皮毛,三年入门也并没有那么容易。”
精益生产本质一个生产方式,在一个被称为“共和国长子”的公司里,在短短的20多年内被学了三次,令人顿生感慨,“我们真正要学就要学到精髓,你不能光学先出车后跳马,回头人家炮就把你吃了。”白宝伦这样解释学习精益生产不能持久或者总是不能成功的原因。
精益生产是一种以通过消除所有环节上的浪费来缩短产品从生产到客户手中时间从而提升企业竞争力的生产方式。天津大学管理学院院长齐二石教授说:“很多人,包括现在的很多书,实际上都不能准确总结丰田生产方式的实质,或者说没有说透。”
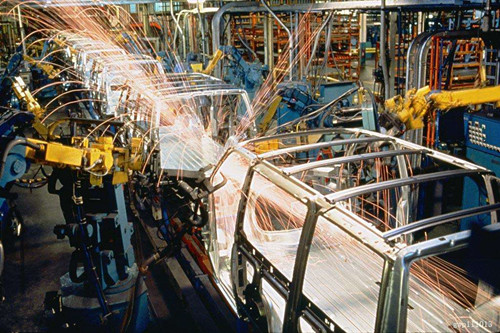
另一支柱为“人字边的自働化(Jidoka)”,与传统追求“高速度、大产量、多用机”的自动化截然不同,它是以最低的成本制造出“适度化、专用化、小型化”的自动机器,以使不仅大批量而且小批量的产品都能够快速合格地被制造出来。
但是在实际的运用中,许多公司仅仅从形式上去效仿某个方面,比如看板管理,而这往往是不能成功的。精益生产是一个系统管理,是一个全员参加的、思想统一的,不断改进的降低成本的系统过程。精益生产的推广从局部试点开始,毫无疑问是正确的,但绝不能局限在局部,不能孤立存在。白宝伦说:“成本管理不能再仅局限于产品的生产制造过程,而是应该将视野向前延伸到原材料、协作件的供应商、延伸到产品的市场,向后延伸到用户的使用、维修和处理。”
对于基础管理落后的中国企业来说,试图一下子运用精益生产无异于痴人说梦。白宝伦说:“供应链这一块现在还不是我们的目标,还达不到。现在解决企业内部的均衡生产,未来才能整合供应链,使整个体系均衡生产。”
推行精益生产需要较好的管理基础,改善是精益生产的基础与条件。推行精益生产,首先要从持续改善入手。天津丰田技术中心在天津一汽丰田推行精益生产,就是先从改善入手,而不是马上推行JIT。因为改善是贯穿于精益生产的产生、成长和成熟的整个过程。JIT的实行需要有较高水平的管理基础做保证。如快速换模,先进的操作方法,合理的物流系统,科学的定额和期量标准,员工素质与设备完好率高等等,所有这些条件必须全部具备,才能实行JIT生产。
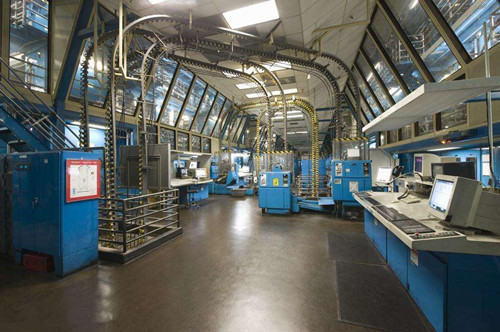
在一汽,已经有工业工程部门的人在为装配线上工人的工作拍摄录像,以分解是否有多余的浪费动作。但是有内部人士认为,他们现在的管理还没有到这个份上,前期的基础太差,管理太粗放了,必须补基础管理。“我们与丰田的差距是20年。我们连走都不会,你想跑,这事情很难。”
严格地说,在入门前进行的管理只能是那些最基础的管理,正如一汽轿车的一位管理人员所说:“如果我们不学精益生产的话,这些工作我们就不做了吗?”
民族性格
尽管如此,丰田汽车还是从美国人的眼皮底下一步步蚕食对方的汽车市场,一汽丰田销售公司总经理董海洋认为,就是这些跨国巨头在精益生产上还是逊丰田一筹。美国人走的是个大规模按照工业工程体系来设计整体模式的这条路。日本人是确立目标不断改进。美国人好讲理论,曰本人讲实务,而精益生产最根本的是要靠现场的细微的改善。他对《环球企业家》说:“你可以阅读伟人的著作,但是你不能因此成为伟人。”
天津丰田技术中心是帮助丰田在华投资企业贯彻精益生产的专门部门。根据他们的介绍,在天津一汽丰田,每一个洗手间里都贴有一张字条,标明节约一度电多少多少钱,节约一滴水多少多少钱。甚至他们的会议室上面都贴有一张纸,把一周每天每个时段哪个部门开会都写得清楚。你开会的时段到了,那对不起,不能开了,必须换人,因为会议是有成本的。这事实上是要求每一名员工都要贯彻精益生产。“如果一个公司只是几个老总在考虑降低成本与一个公司几千人都在考虑降低成本,哪个有效?”
曾经三次陪同丰田汽车在中国投资企业的经理人到日本去研究精益生产的齐二石教授认为,中国企业中的凝聚力和责任心的缺乏也是精益生产难以推行的重要原因。丰田公司没有一个质检员,但是每一个人都是质检员,他们是自检和互检。中国的企业文化和生活背景不要说自检,互检都不行,它容易造成员工之间的矛盾和隔阂。“本来和他就有矛盾,你让他来检查我的,越检查矛盾越大,我就故意给你找茬。”
讲述这个经历的白宝伦说:“应该学习他们现地现物、一丝不苟的敬业精神;学习他们不找借口,把握现状的务实精神。”
谈到这个方面,也许有些人感到吃惊,中国已经进入工业社会甚至有些地区已跨入知识经济层面,再谈农业经济思想的影响是否太不可思义。根据本人多年的咨询经历,发现中国的大部分地区的经济结构仍然是很落后的,尤其是员工的思想理念仍然是农业经济的思想,具体表现为心态封闭、做事粗放、看问题基于个人角度而不是组织层面。在日常工作中喜欢积压材料、被动的工作心态也正是农业经济思想的表现。
目前中国企业的一些不合理现象很大程度上归因于这个方面。中国企业要实现突破面临很多困难和瓶颈,本人认为在这些困难中员工思想理念的转变是首当其冲的,毫不夸张地说如何将员工的“农业思想”转变成“工业思想”,或者说如何将“农民”快速转变成“现代产业工人”是决定企业能否快速发展的关键因素。
文章来自网络,版权归作者所有,如有侵权请联系删除