“TPS”这个频频见诸报端的字眼,几十年前在全球汽车制造业激起了惊涛骇浪,让昔日汽车工业诸位老大纷纷放下身段,竞相研究甚至效仿这匹“黑马”的后发制人的秘诀——丰田独特的精益生产方式。TPS(丰田生产模式)作为一种文化,已经深入到了广州丰田生产和运营的每一个环节中。除了自动化、标准化和持续改善之外,它的精髓还在于准时化生产(Just In Time,缩写为JIT),以“零库存”为目标,极力提倡减少库存。在广丰的眼中,企业运行时的“库存”是最大的浪费。
环环相扣的拉动式生产
汽车工业的传统思考方式是“前一道工序向后一道工序供应工件。”这种传送带式的大批量的盲目生产,往往会造成过度生产的浪费、搬运的浪费、库存的浪费、加工本身的浪费及等待的浪费等。
为了彻底消除浪费,早期的丰田在美国“自选超市方式”的启发下,把超市看作生产线上的前一道工序,顾客购买相当于后一道工序,他们在需要的时间买需要数量的商品,而超市将立即补充顾客买走的那一部分商品。丰田经过实际生产中的不断完善与调校后,拉动式生产(Pull System)应运而生,即“由后一道工序在需要的时刻到前一道工序去领取需要数量的特定零部件,而前一道工序则只生产所需要领取的数量。”
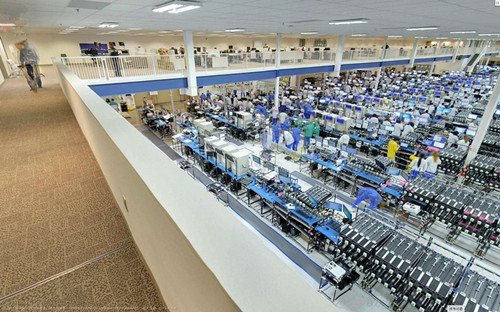
因此,在广州丰田的总装车间,看不到分门别类堆积在物架上的零部件,也见不到其他工厂“零部件搬运工往来穿梭”的繁忙景象。这都归功于丰田SPS(对装配线成套供给零部件)体系,即每一个物料架紧随一辆等待装配的车身,总装工人只需在物料架和车身同步流动的平台上,将触手可及的零部件对号入座装配上车身即可,连工人转身取物料的时间都省了。“通过对零部件采取这种‘配餐式’的供应,在必要的时间内生产必要数量的产品,是丰田精益生产方式所倡导的。”广州丰田高层曾表示。因此广州丰田无论整车还是零部件,都能实现“零库存”的管理目标,同时也掀起了“60秒生产一辆凯美瑞”的新一轮效率革命,兑现了“顾客买多少,就送多少到顾客手上”的承诺。
看板方式成“独创利器”
广州丰田不仅引进了丰田最先进的设备和人才,还引进了生产中非常重要的一环:看板方式。根据拉动式生产的实际情况,把生产计划下达给最后的组装线,在指定的时间生产指定数量的指定车型,组装线便依次向前一道工序领取所需要的各种零部件。在这过程中,“用于领取工件或者传达生产指令的媒介”就是为拉动式生产而量身定做的“看板方式”。
“思路其实很简单。看板记录了所需物品的信息内容,广丰的所有生产人员都根据看板所显示的信息,来生产零部件或完成品,它起到了传递生产和运送指令、调节生产均衡、改善运营机制等作用。看板方式是从丰田汽车的零部件生产开始的,但它的优越性使其在全工程里扩展开来,已经成为了丰田汽车的中枢神
经。”据业内有关人士表示。
“带人字边的自动化”造就高效率
除了引进丰田全球领先的生产设备,实现了工程的高度自动化,同时在广州丰田,还有一个专有名词“带人字边的自动化”,它来自丰田的一个生产理念:先进的设备只是起点,人才是品质的最终保障。
据了解,早在工厂尚未建成之前,广州丰田就先期投资1千多万元建设了员工的技能训练场,对每一个岗位员工都进行基本技能训练,同时,还派出了大批班、组长、高技能人员到日本接受严格的现场管理及技术培训,让他们的管理水平、专业技能得到更高的提升;为了确保生产品质,公司在投产初期,还邀请了众多日本专家进驻广州丰田,现场作业、现场指导工作。
值得一提的是,丰田还一反传统生产系统中的“定员制”,根据生产量的变动,弹性地增减各生产线的作业人数,运用较少的人员资源完成更多的生产活动,这就对作业人员提出了更高的要求。为了适应人员弹性配置的方法,广州丰田的员工通过专业化的技能培训成为了身怀各种技能的“多面手”,使广州丰田的生产效率达到了极高的水准。
一位汽车行业营销研究专家曾针对丰田准时化(JIT)生产方式表示:“在没有库存的情况下,客户需要多少产品,丰田就会第一时间生产多少产品,这与超市中顾客购买商品后的货品补充如出一辙。启动准时化系统按钮的那个角色总是顾客。”
文章来自网络,版权归作者所有,如有侵权请联系删除